“TLMX” Lock-Stitch Chenille Taping & Coiling Embroidery Machines
The TLMX series of lock-stitch chenille embroidery machines can sew and secure strip materials such as cord and tape. They can handle special embroidery processes such as cording, taping, zigzag swing stitching, and coiling.
The technology for sewing and securing cords has expanded to other fields such as apparel, automobiles, and housing. These machines are suited to a wide range of applications, from decorative to functional embroidery.
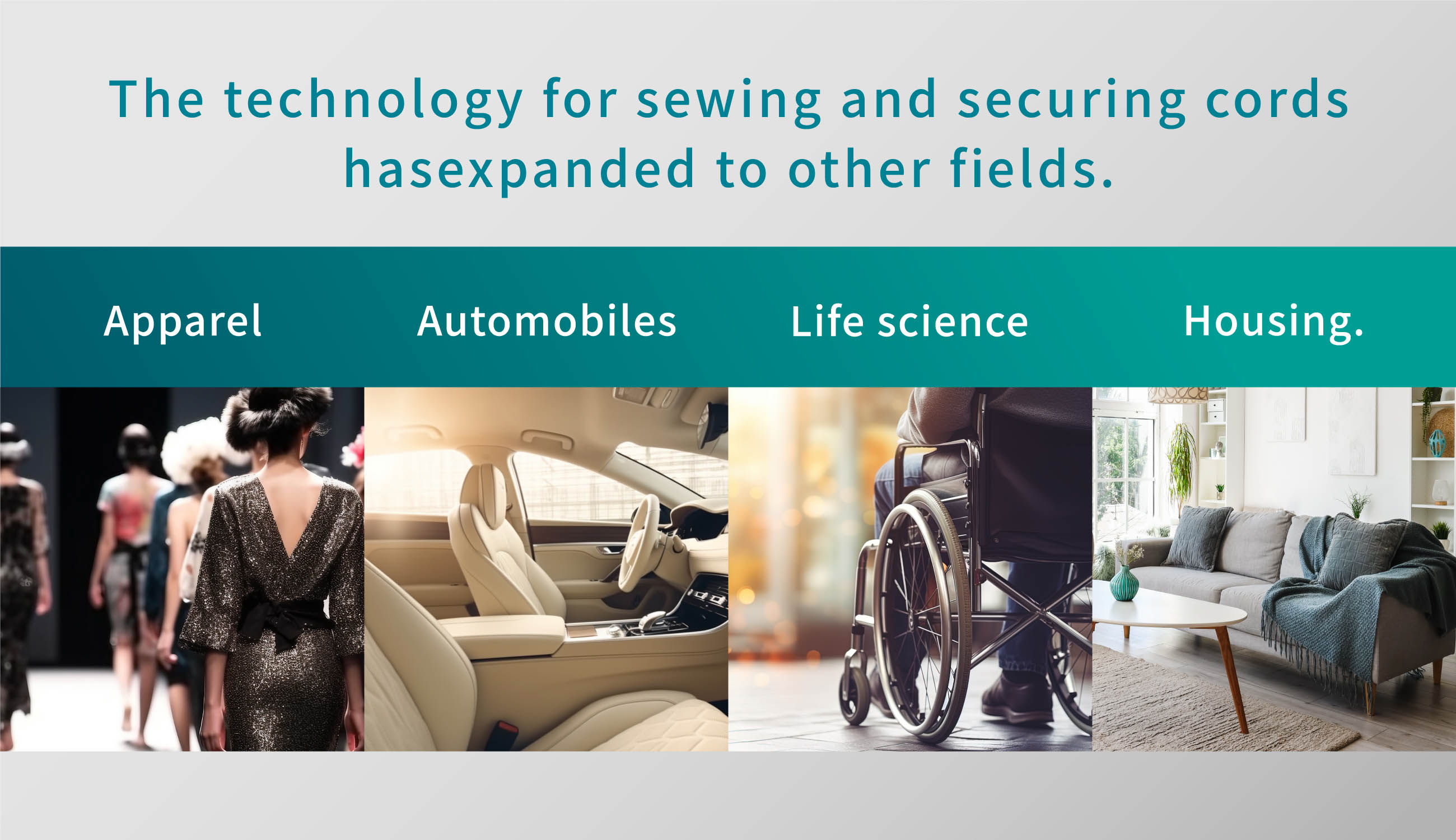
Create Splendid Embroidery Arrangements with Cord or Tape Materials
These machines incorporate a number of cutting-edge technologies for reliable sewing with many different materials. The high-speed rotation enables more stable sewing. A wide variety of embroidery arrangements can be made using cord and tape materials.
Taping Embroidery
Use the standard and optional guides to sew all kinds of tape materials.
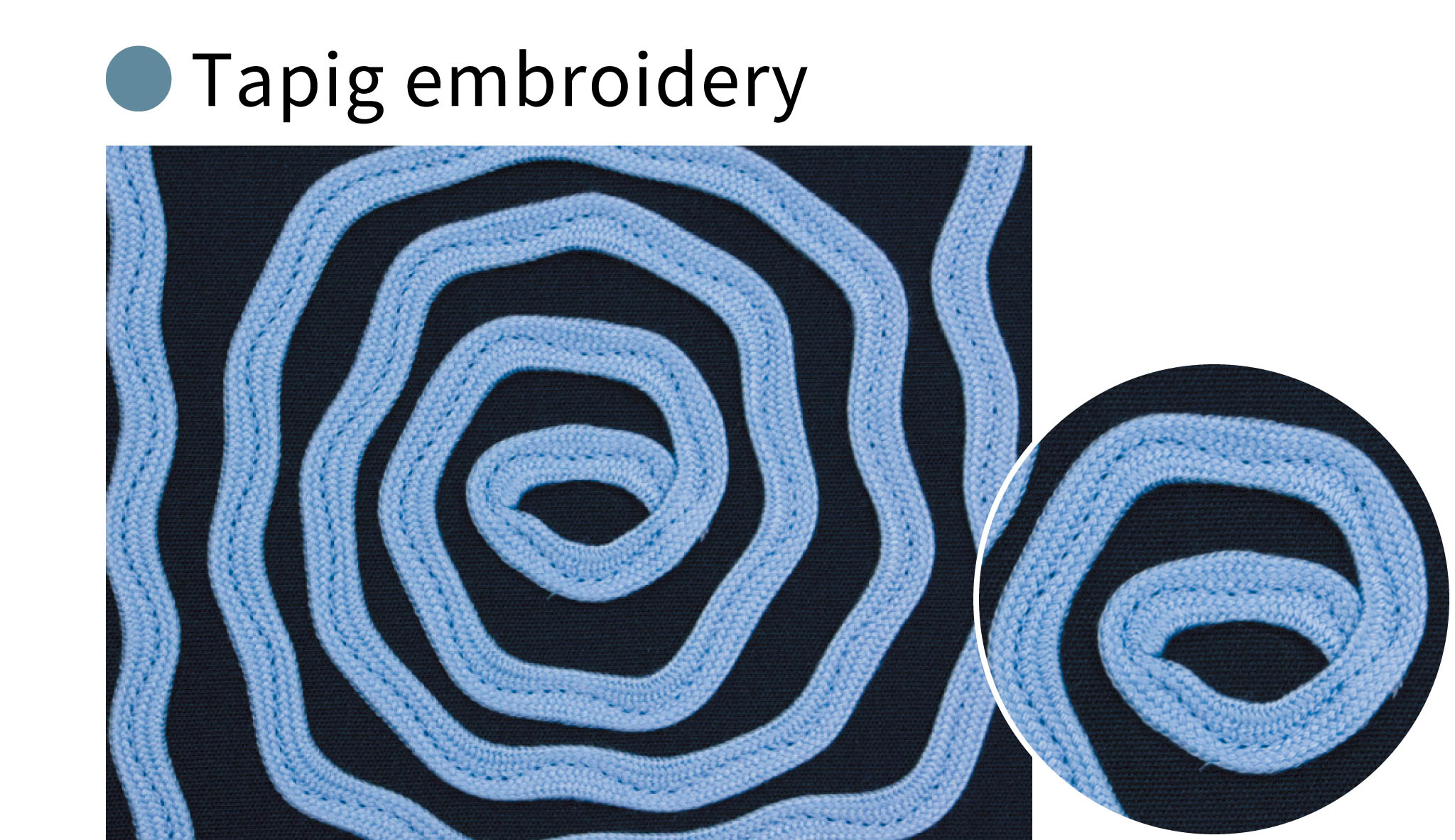
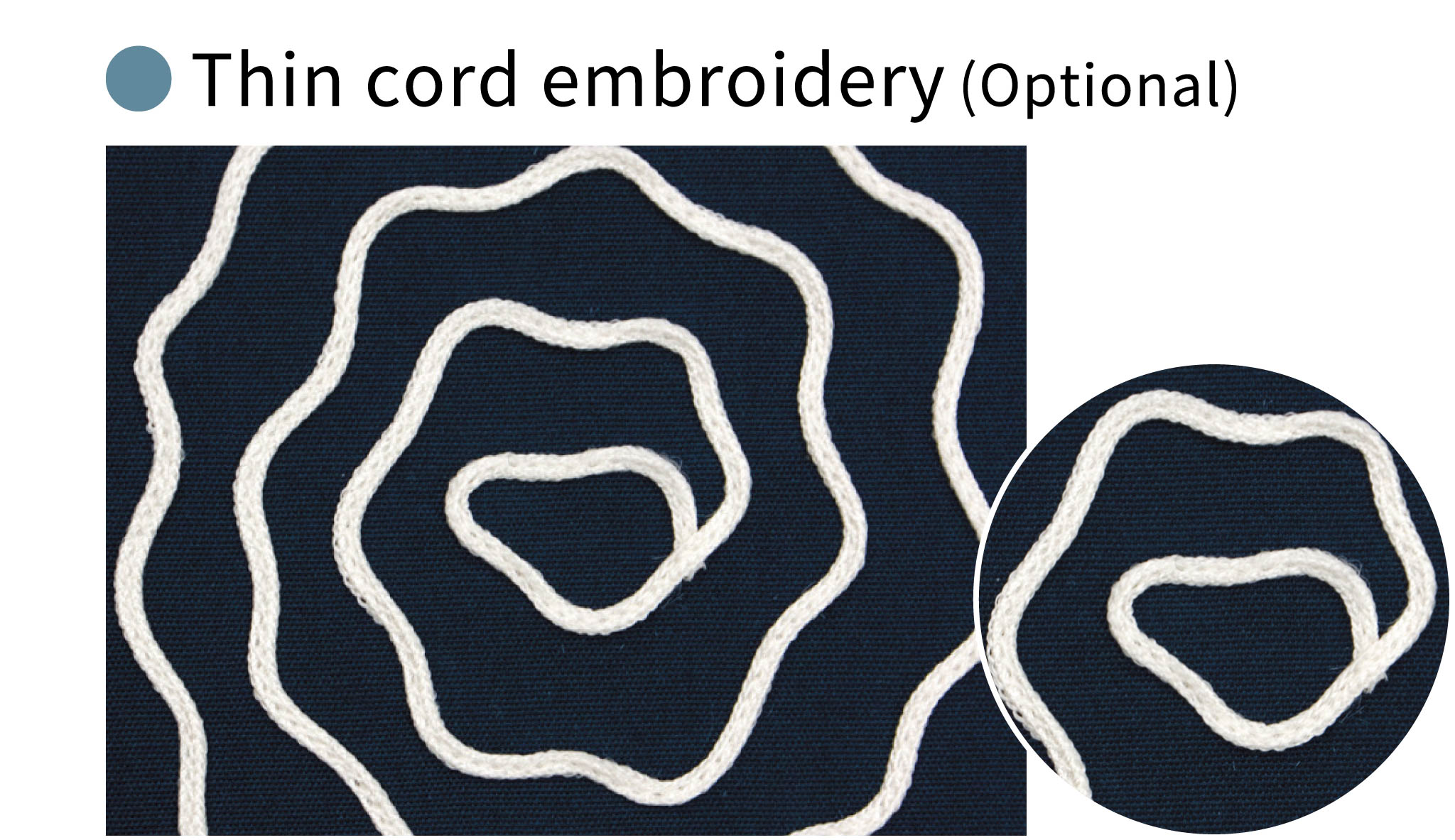
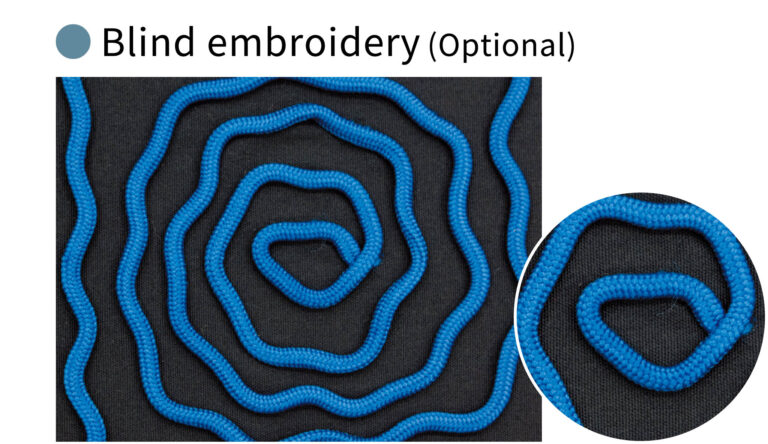
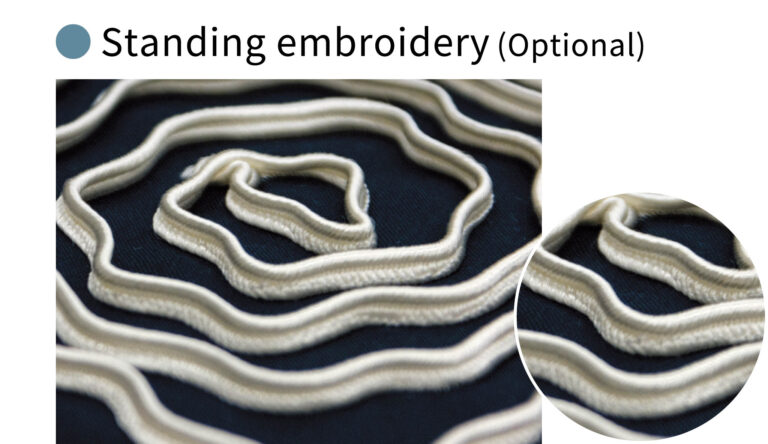
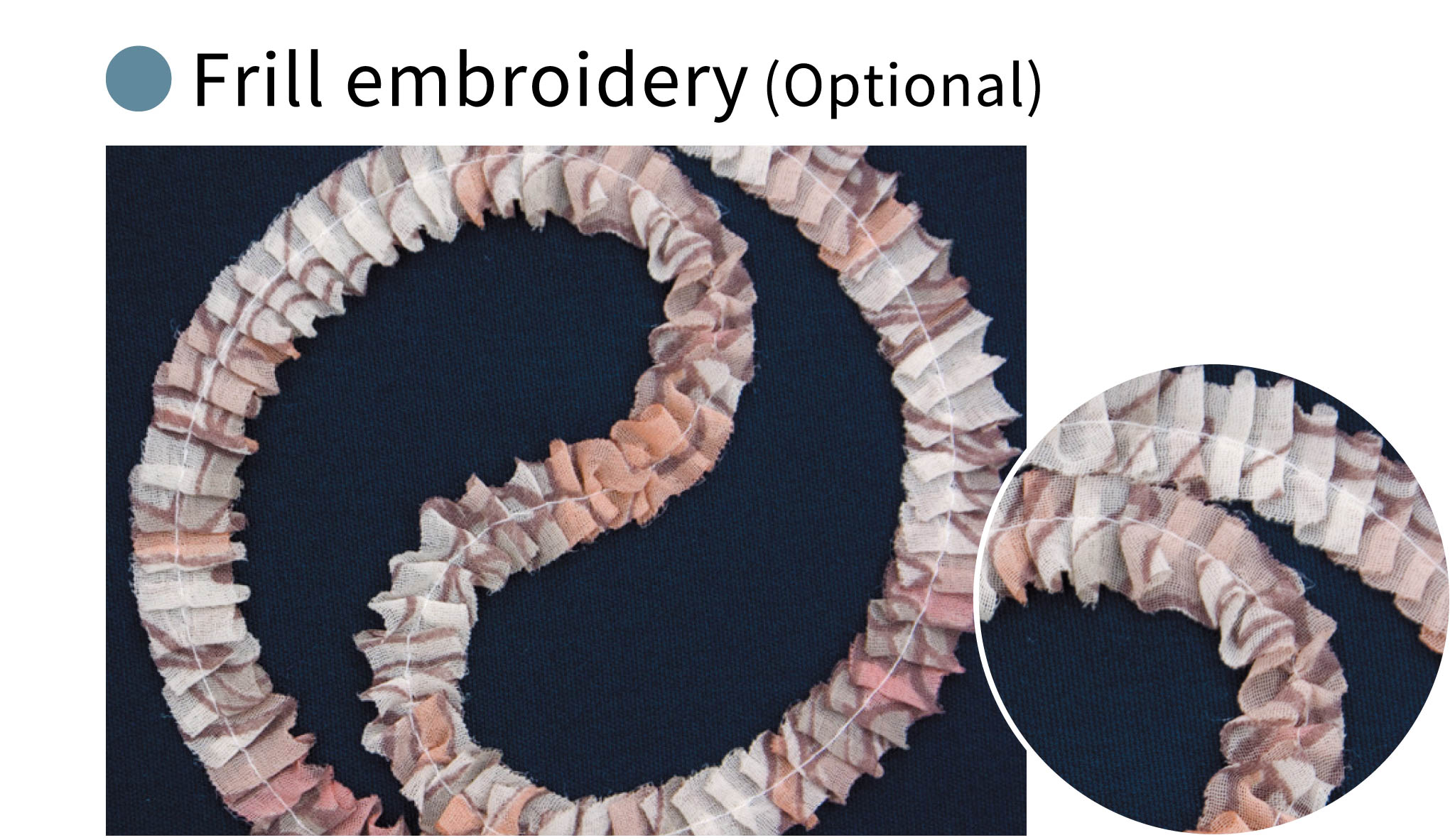
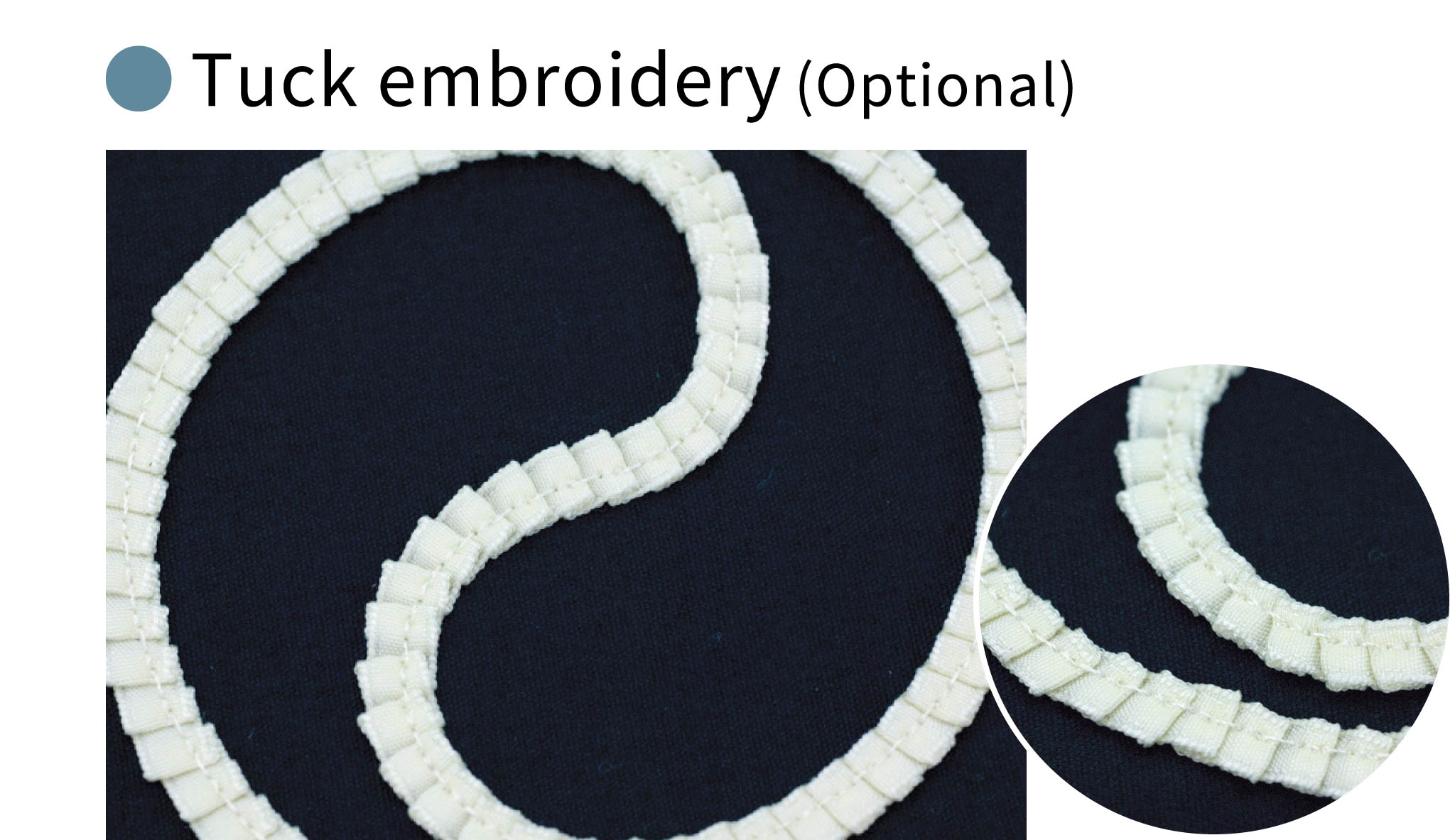
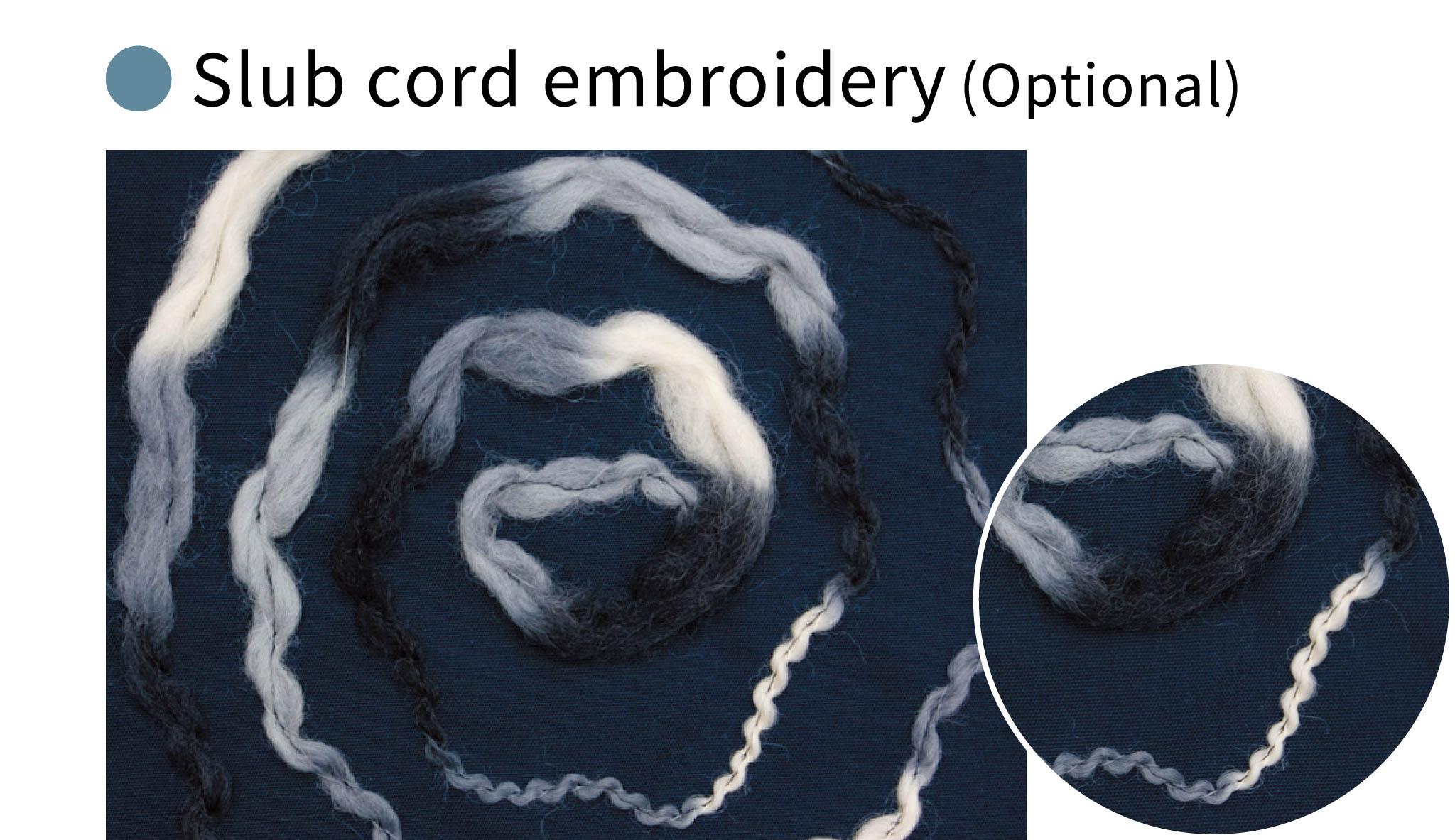
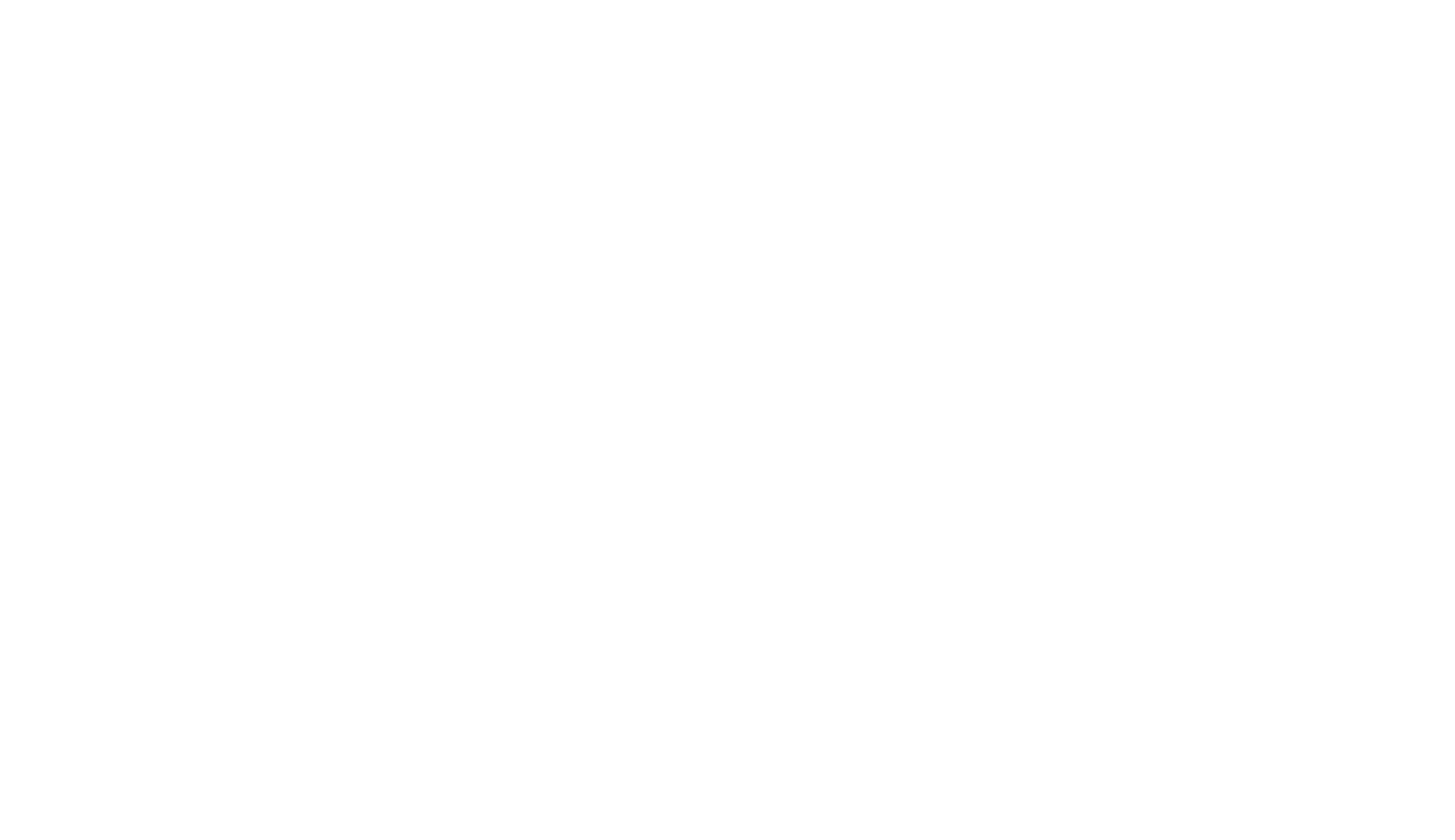
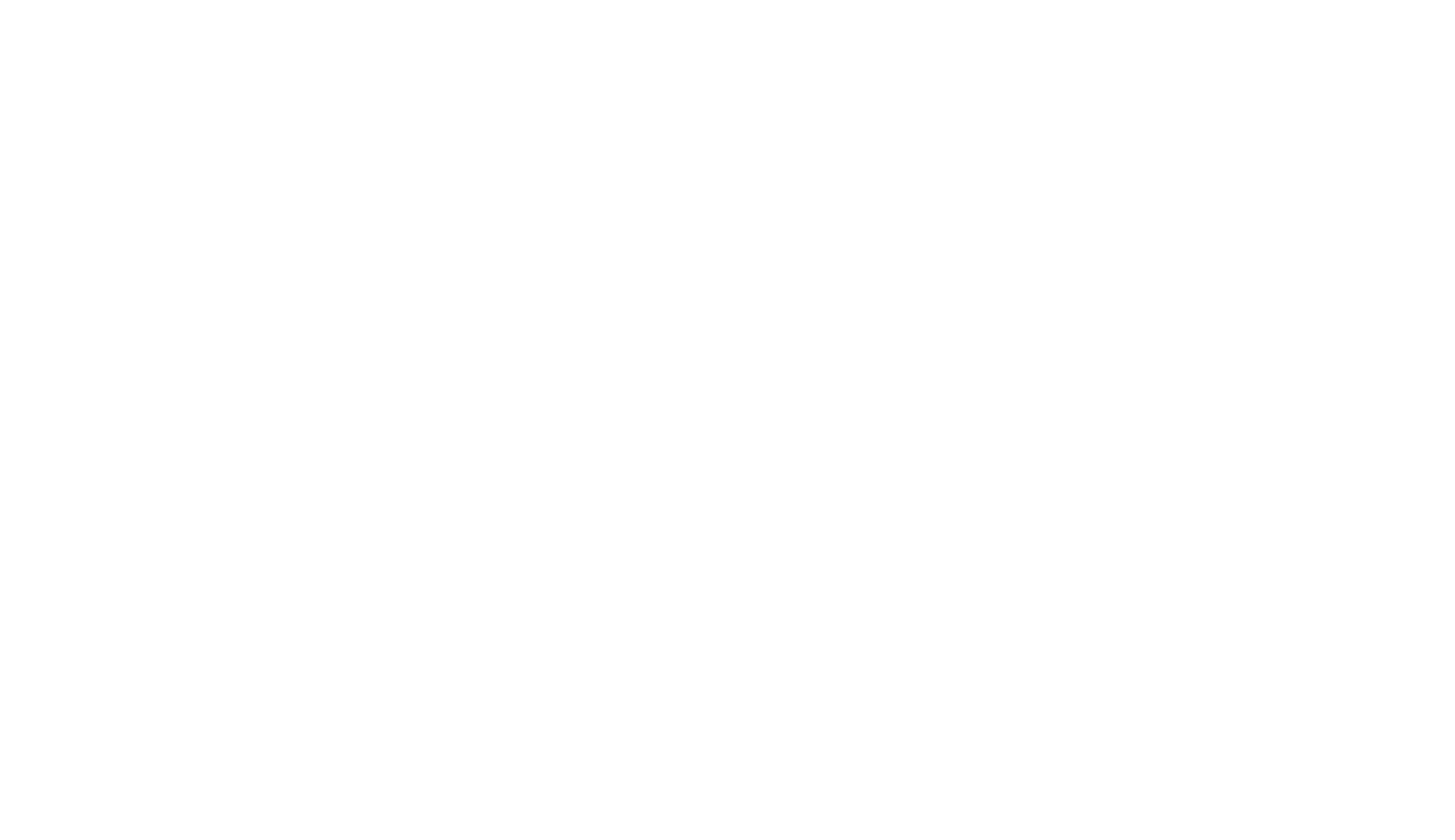
Zigzag Swing Stitching
Use the using zigzag swing attachment to swing the zigzag lever from side to side above the material while sewing. Works with thin materials, extra-thick materials, sequin materials, and other decorative materials.
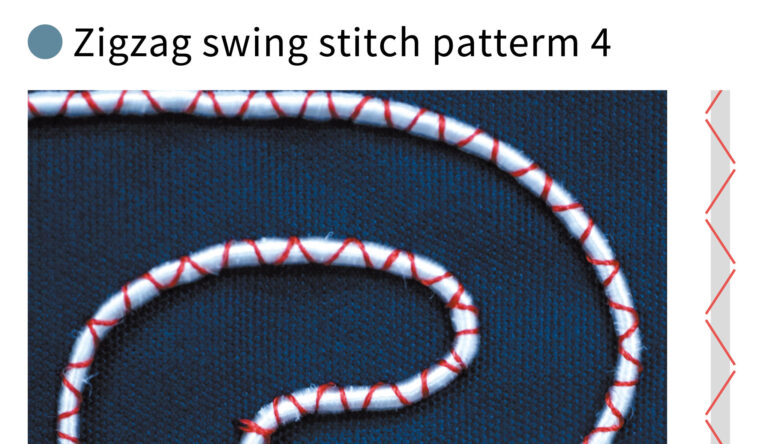
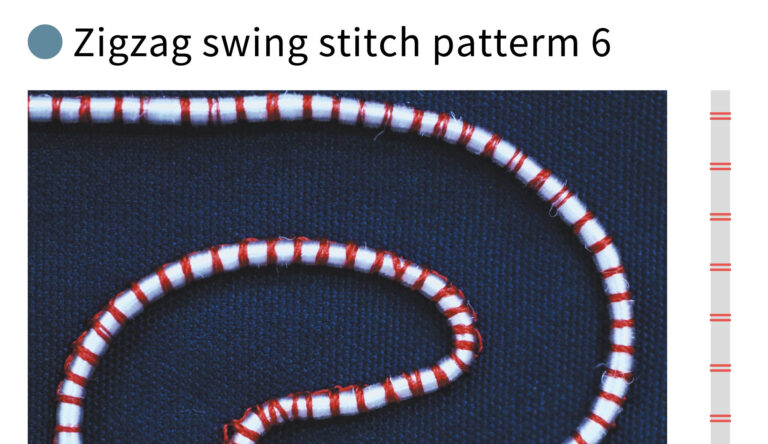
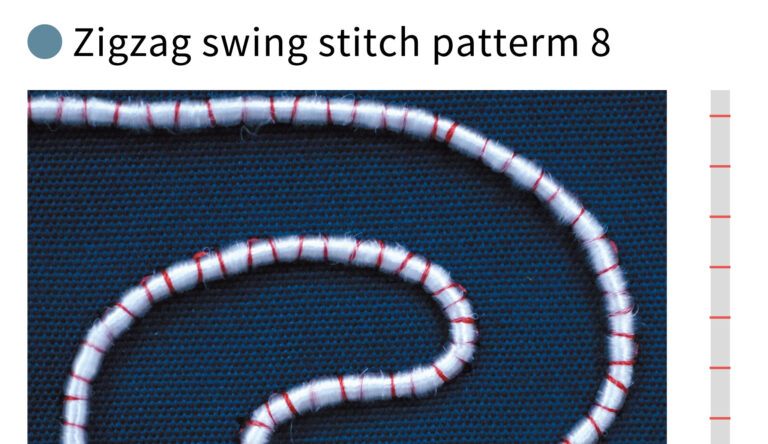
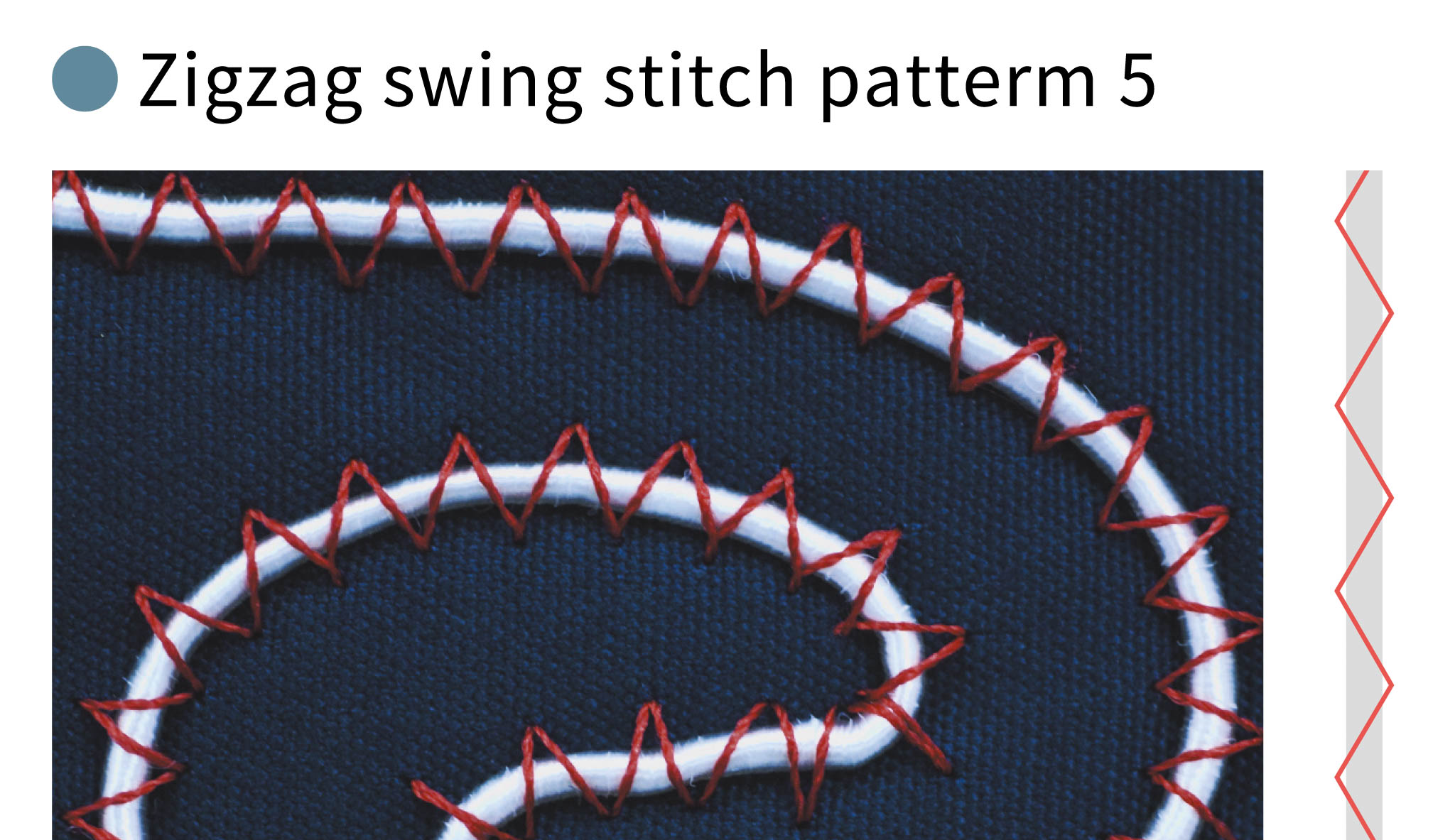
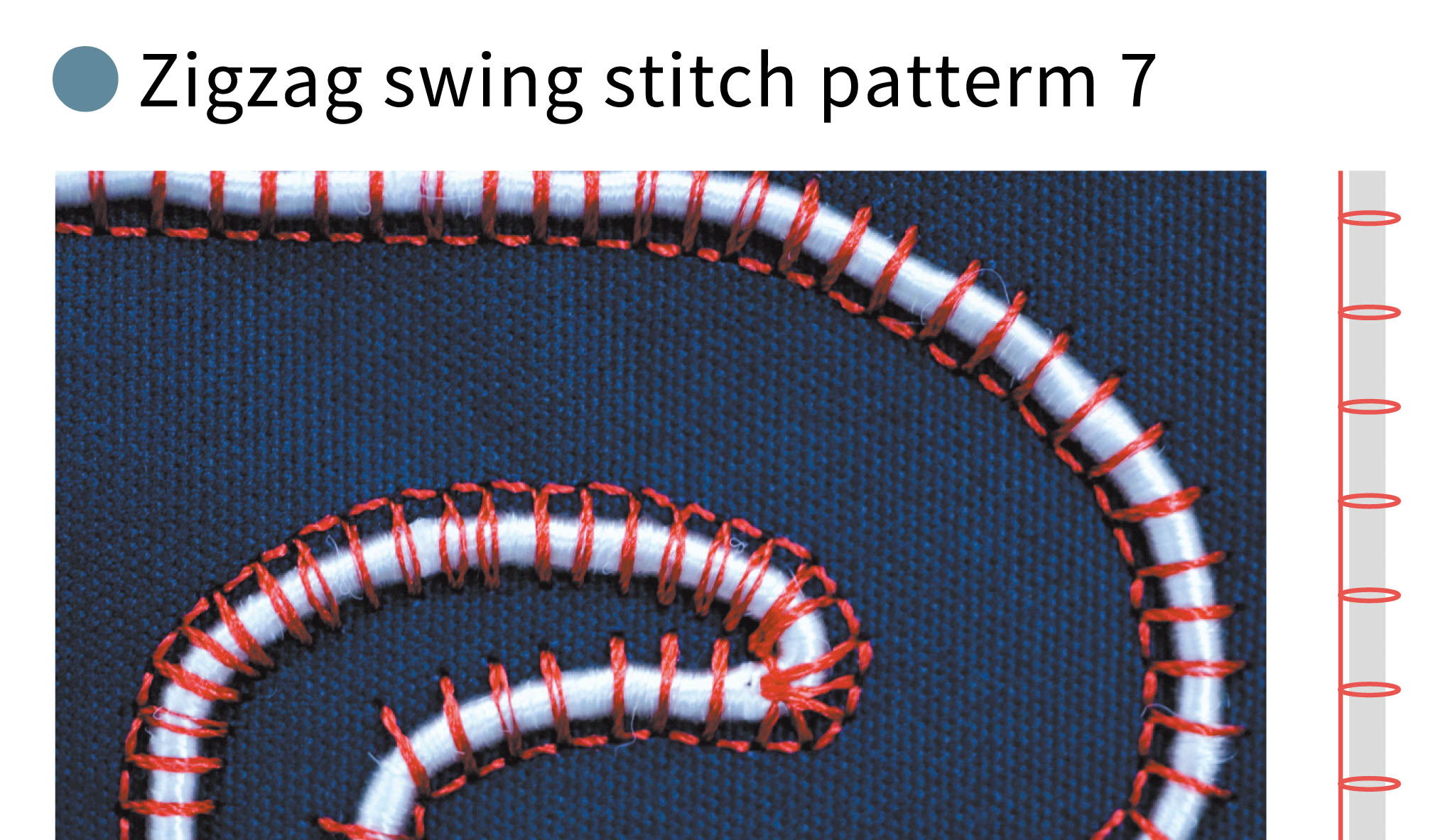
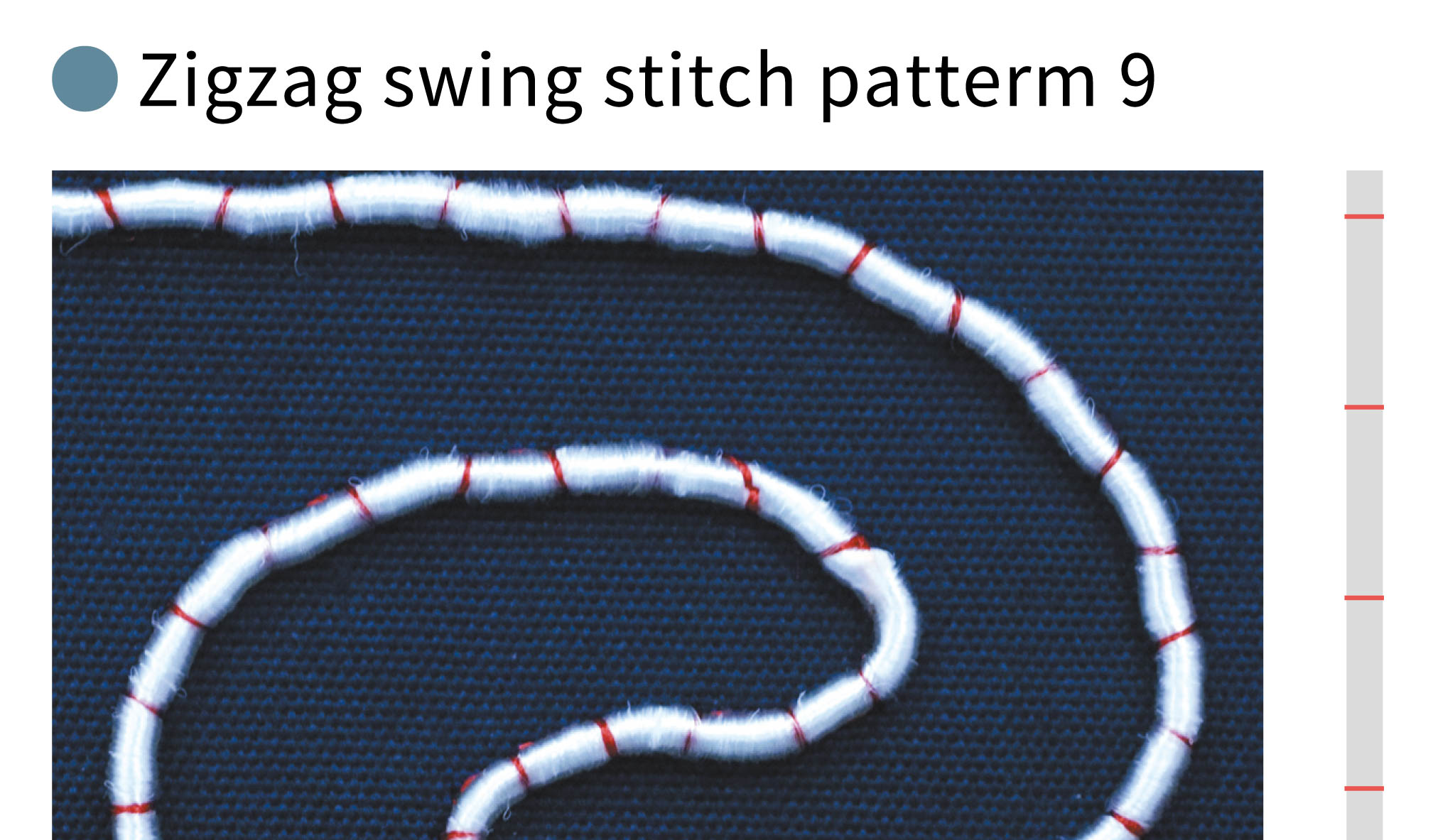
Coiling Embroidery
3 kinds of materials are used: embroidery thread, core thread, and coiling thread. Core thread is stitched while it is wound by coiling thread.
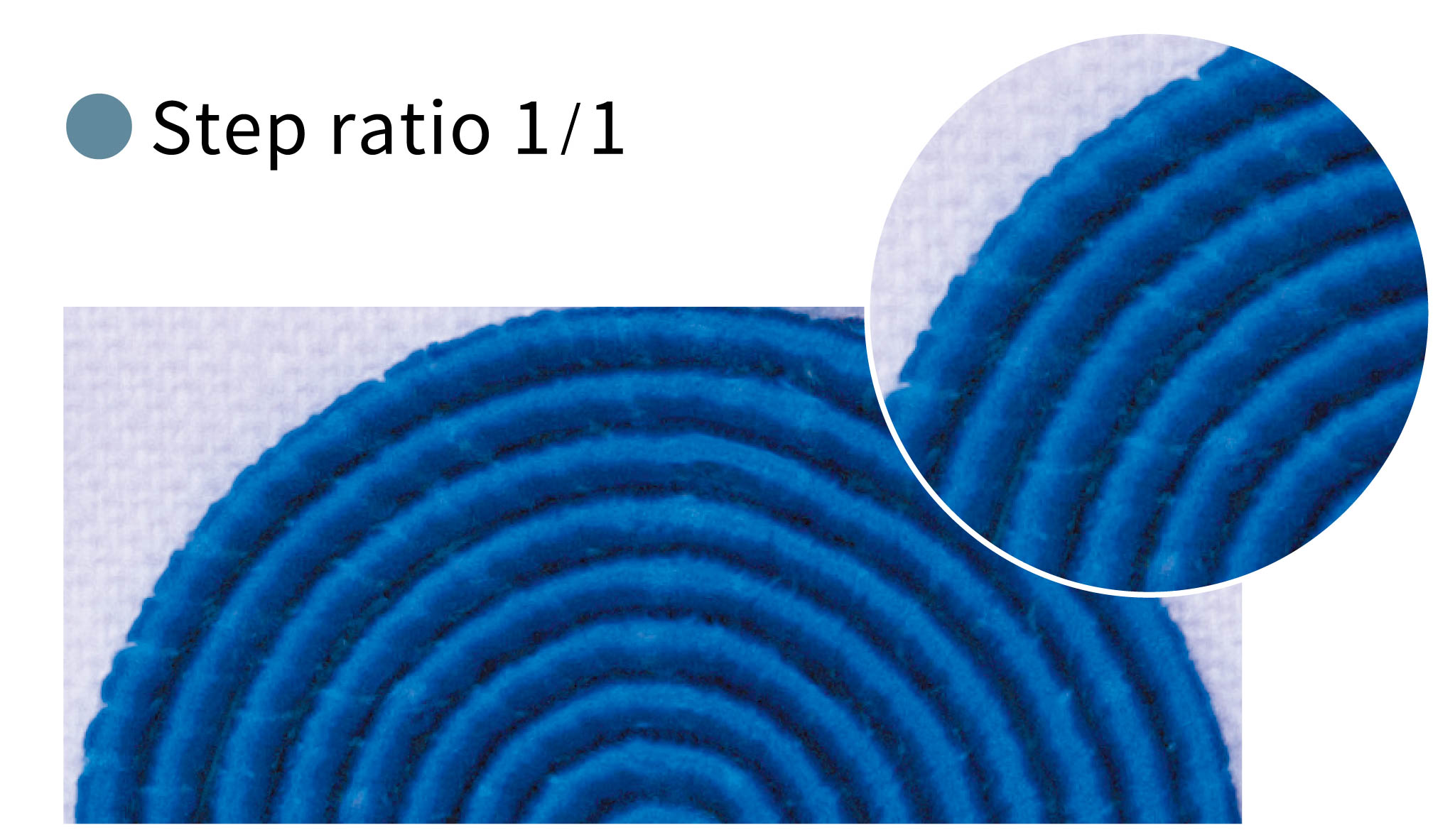
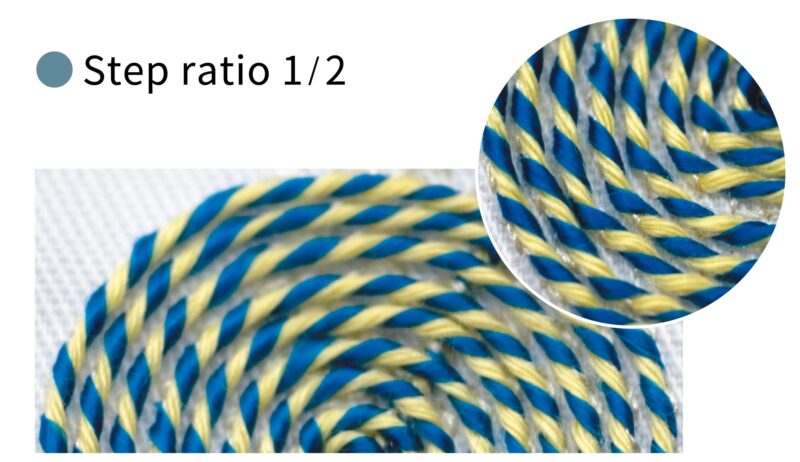
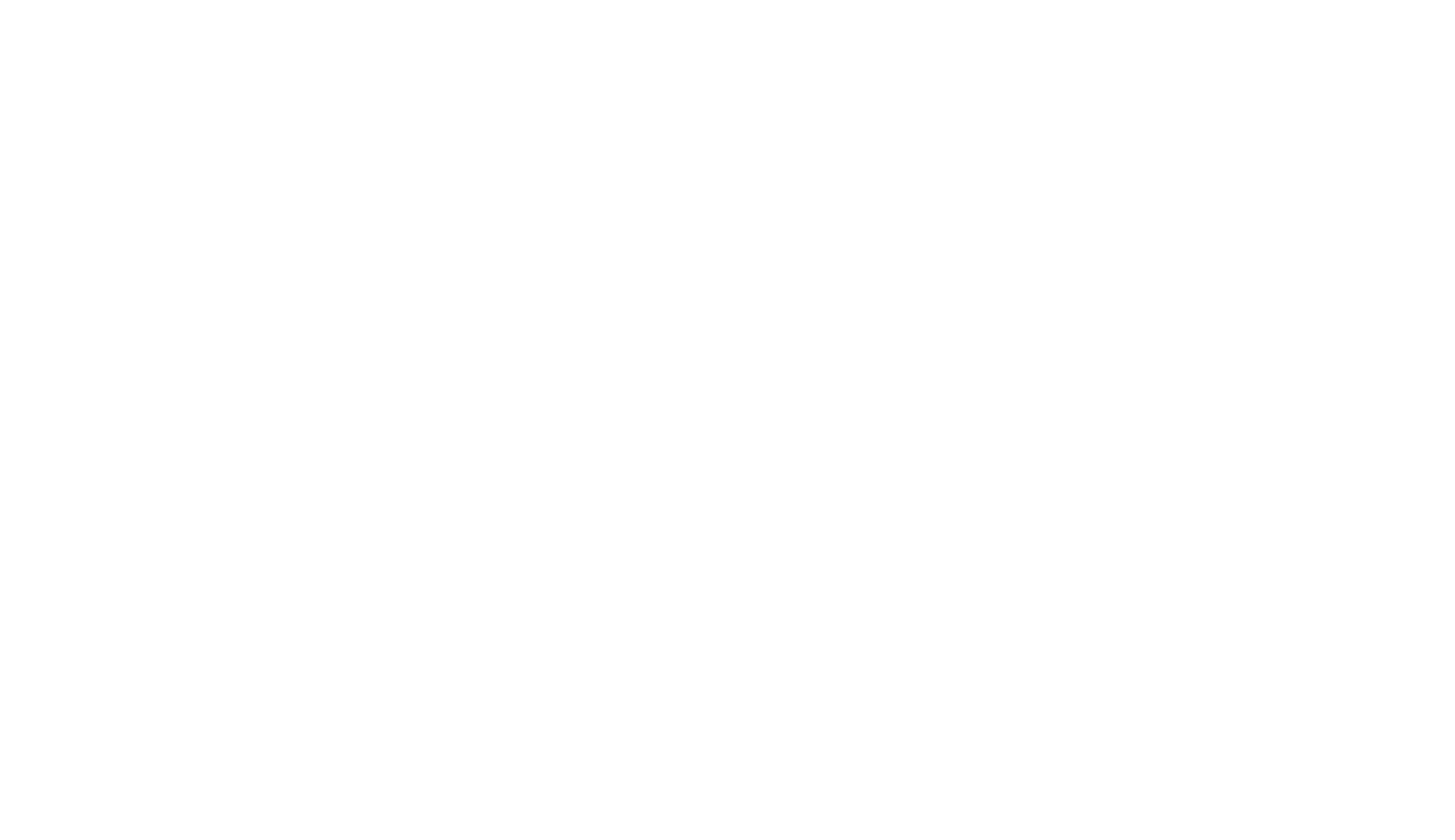
For functional embroidery and sewing on special materials such as heater wire, optical fiber, etc.
Tajima’s proprietary technology allows you to securely sew on special-purpose materials such as heater wires, optical fibers, and artificial muscle. Conventional methods of sewing on heater wire pose a risk of breaking the wire when pressure is applied to the fabric, but with Tajima machines, the fabric is fixed in the frame. The frame moves in a zigzag pattern under the needle to sew on the heater wire—without breaking it—which enhances the durability of the product.
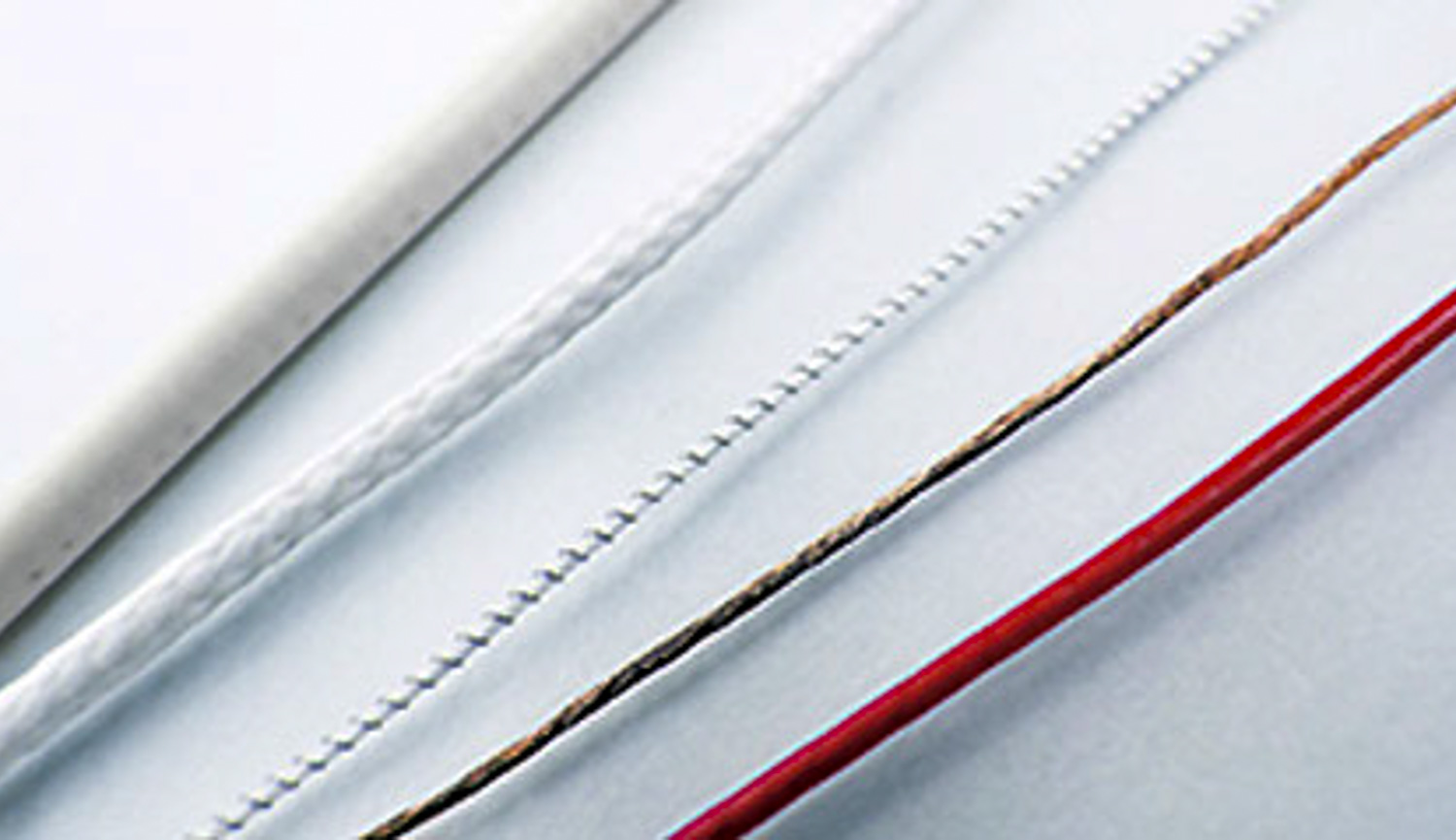
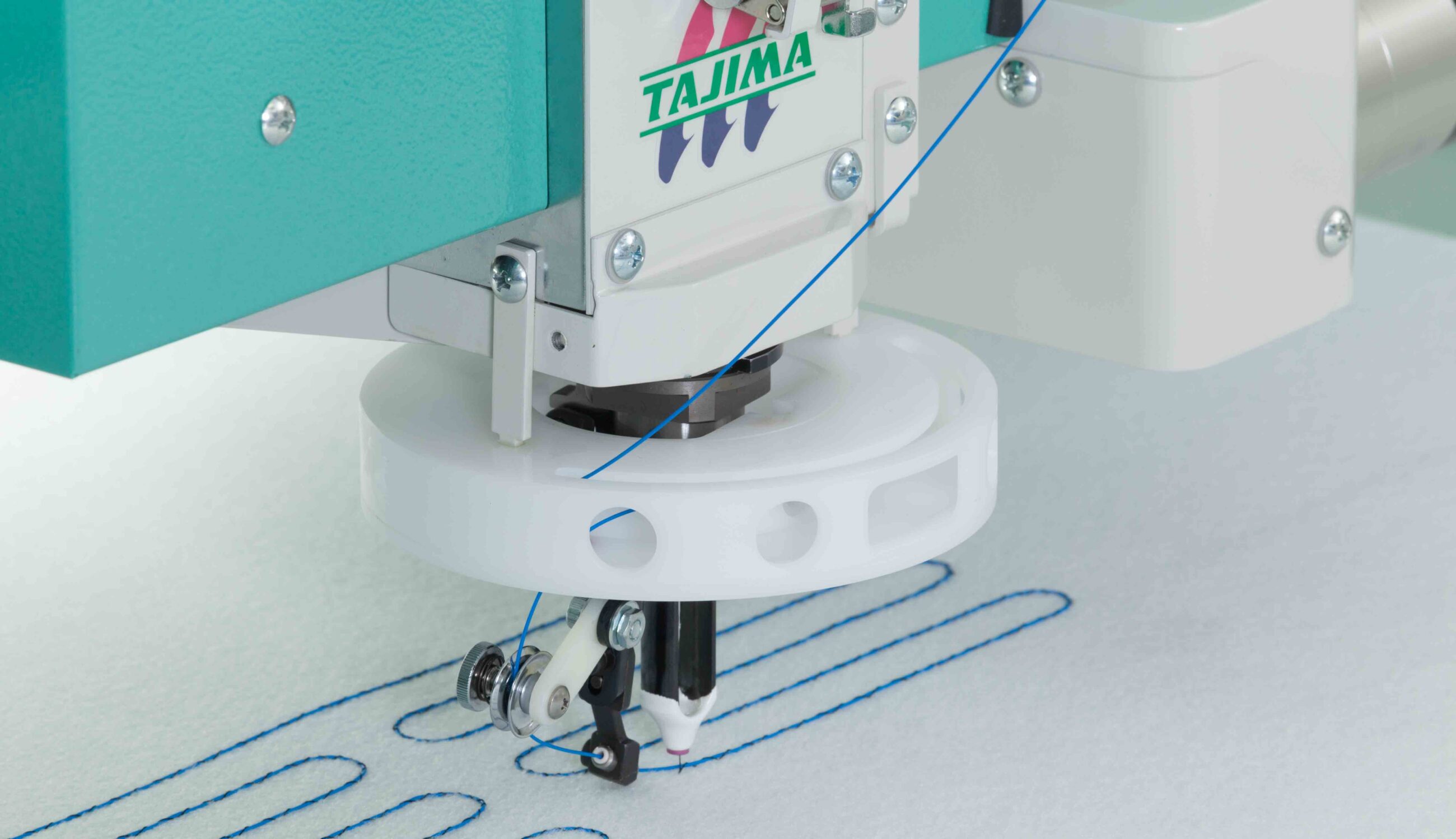
User-Friendly Design
High-speed rotation up to 1,000 rpm
The machines achieve high speed rotation of up to 1,000 rpm for tape and zigzag stitching and up to 500 rpm for coiling.
Easily replaceable attachments
Attachments for taping, coiling, and zigzag stitching can be easily replaced with a single screw.
Attachments improve productivity
The double bobbin attachment enables sewing and taping to be performed at the same time.
Swing interval optimized for the particular materials
The zigzag swing interval can be set to a maximum of 16 mm. Rotating the M-axis as well (Zigzag Swing Assist; Pat. Pend.) produces a beautiful finish.
Adjustable N-Pipe stroke for different materials
The bottom dead center position is freely adjustable to accommodate beaded cords and other special materials.
Automatic retraction function enhances efficiency
The N-Pipe and presser foot automatically retract when embroidering is finished. This facilitates work when changing fabrics and switching frames.
Tajima’s Customer Support Services
Sales in 160 countries and regions around the world.
We have delivered machines to 160 countries and regions and have a worldwide service network. Replacing embroidery machines or starting a new embroidery business? We apply Tajima’s proprietary AI technology and software in helping resolve our customers’ business issues. Please feel free to contact us through the CONTACT form.
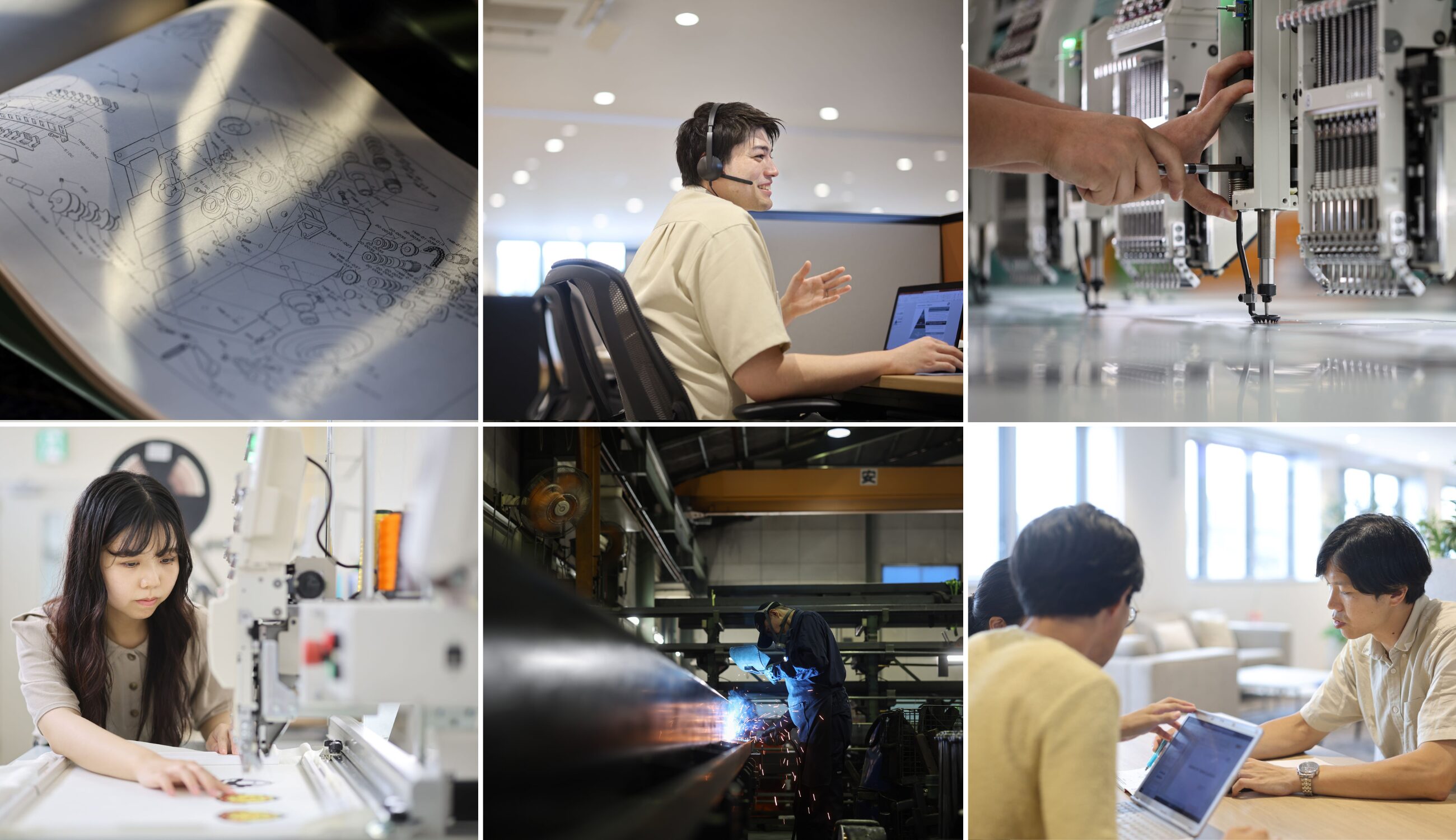
TLMX
TLMX Product Specifications
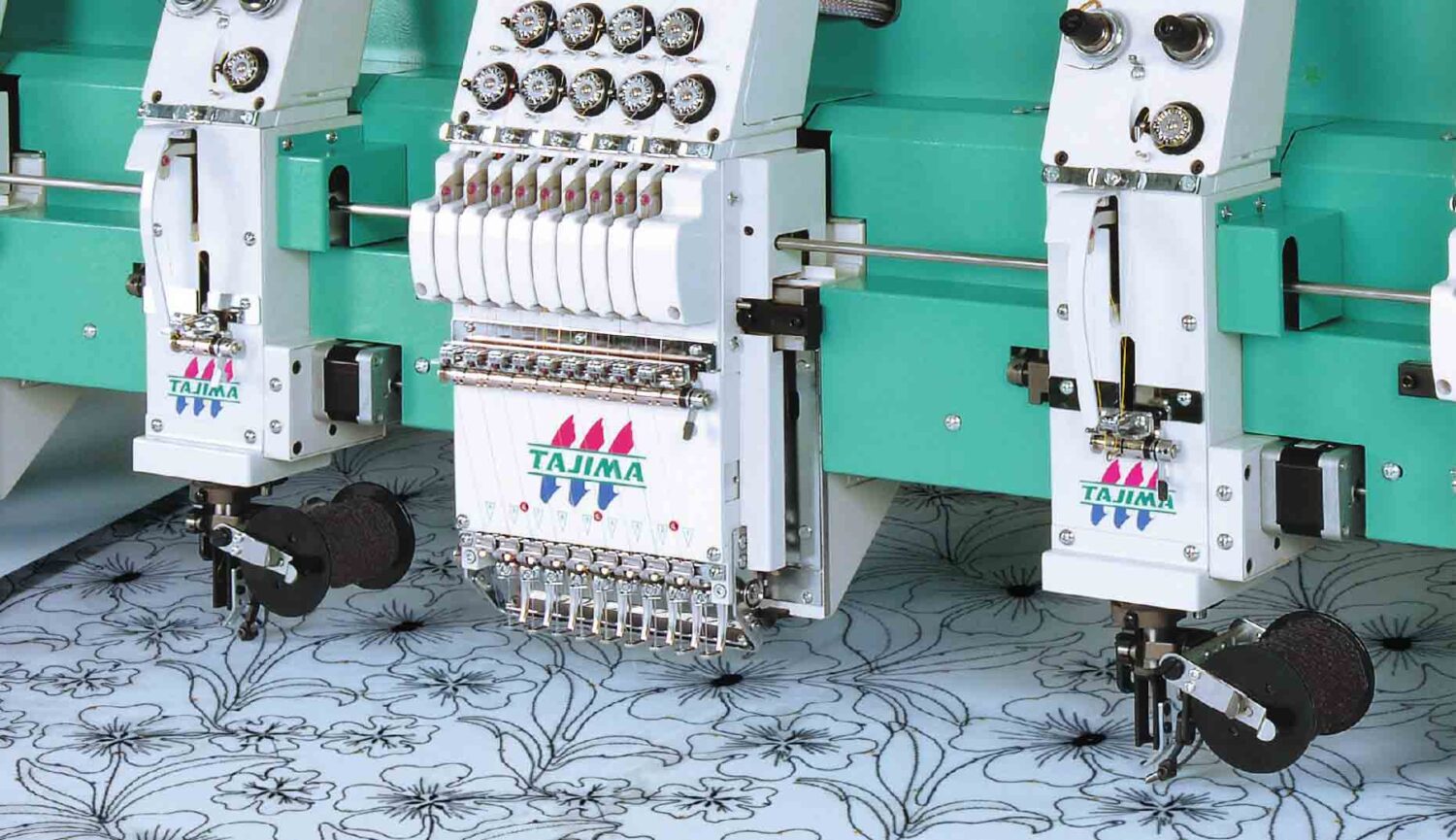
TLMX Mixed Type
A mixed type, integrating lock-stitch chenille embroidery heads and standard embroidery heads in pairs.
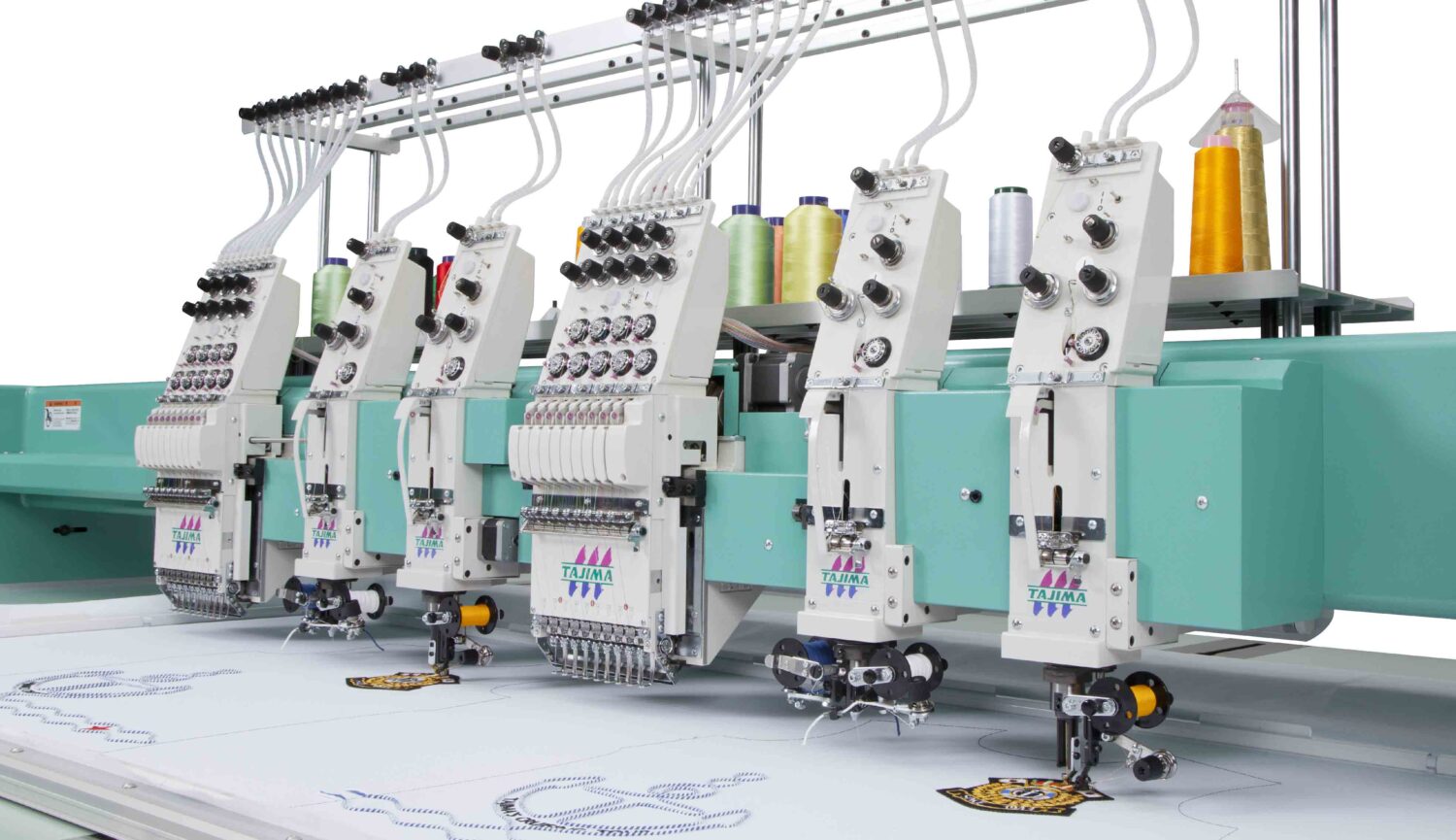
TLMX Triple Mix Type
The triple mixed type joins two lock-stitch chenille embroidery heads and a standard embroidery head.
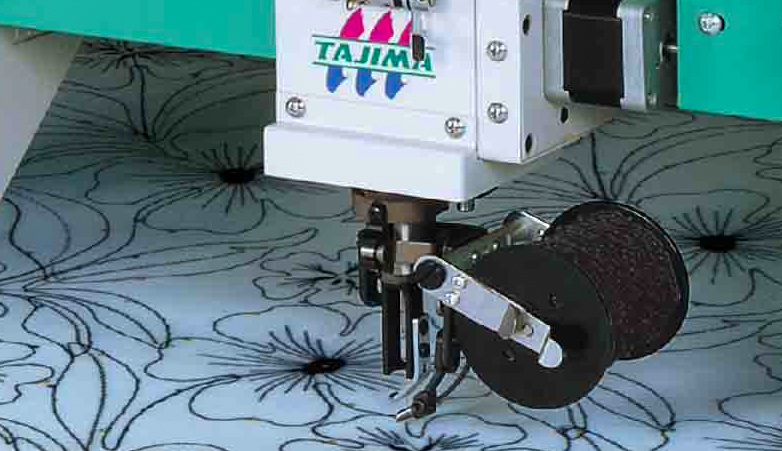
TLMX 100/T00 Type
The 100 series uses lock-stitch chenille embroidery heads exclusively.
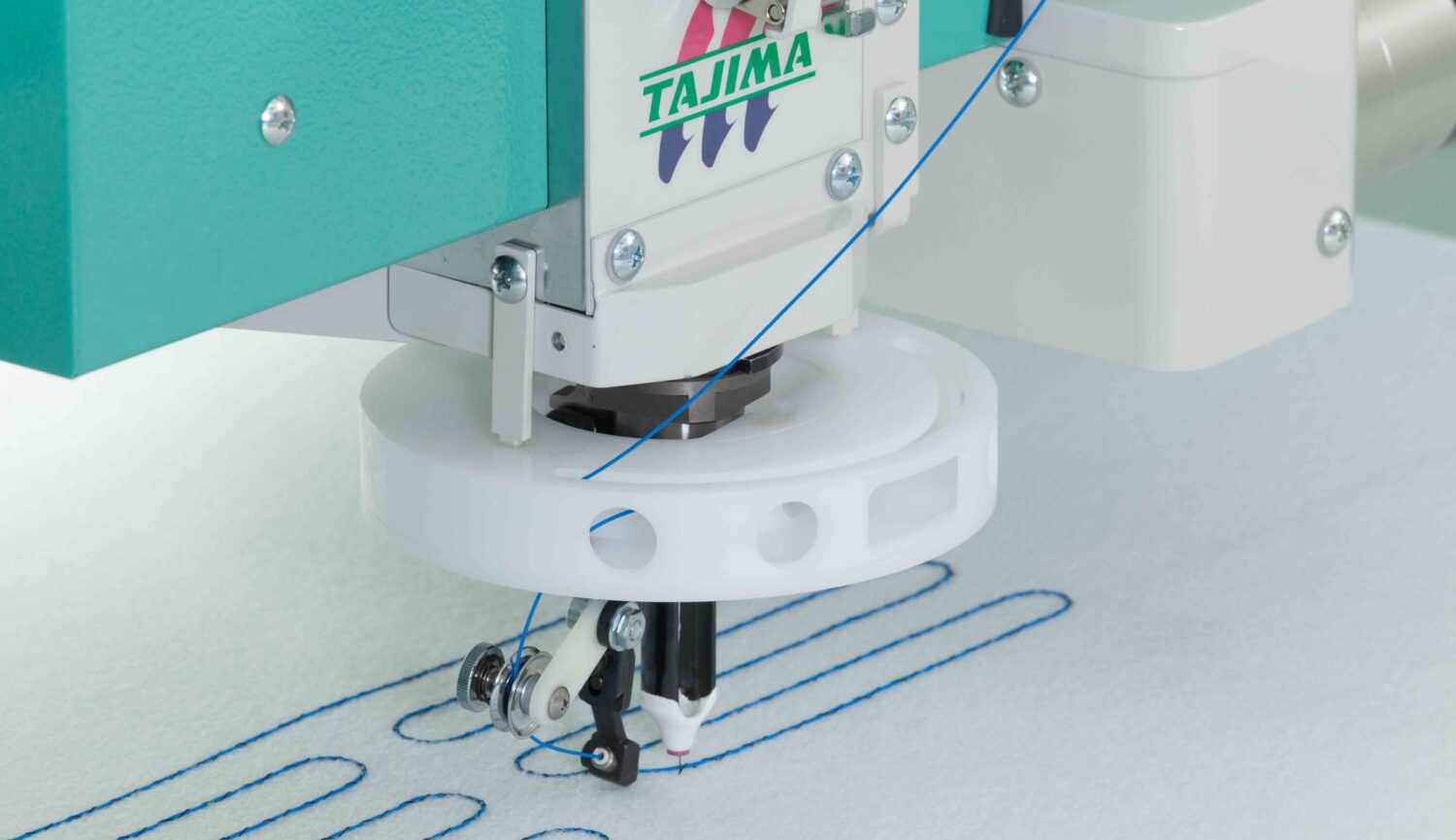
TLMX Heater Wire Sewing
TLMX Mix Type/Triple Mix Type
Model | Multicolor heads Needles | Lock-stitch chenille heads |
Multi color heads | Head interval |
Embroidery field (D×W) | Embroidery field (Continuous) | Overall Width | Depth | Height |
---|---|---|---|---|---|---|---|---|---|
TLMX-904 | 9 | 4 | 4 | 550 | 680×550(230) mm 26.7×21.6(9.0) inch |
2,200 mm 86.6 inch |
4,045 mm 159.2 inch |
1,800 mm 70.8 inch |
1,540 mm 60.6 inch |
TLMX-915 | 9 | 15 | 15 | 550 | 850×550(230)mm 33.4×21.6(9.0) inch |
8,250 mm 324.8 inch |
10,295 mm 405.3 inch |
2,140 mm 84.2 inch |
1,730 mm 68.1 inch |
9 | 15 | 15 | 550 | 1,000×550(230) mm 39.3×21.6(9.0) inch |
8,250 mm 324.8 inch |
10,295 mm 405.3 inch |
2,440 mm 96.0 inch |
1,730 mm 68.1 inch |
|
9 | 15 | 15 | 550 | 1,200×550(230) mm 47.2×21.6(9.0) inch |
8,250 mm 324.8 inch |
10,295 mm 405.3 inch |
2,840 mm 111.8 inch |
1,730 mm 68.1 inch |
|
9 | 15 | 15 | 550 | 1,500×550(230) mm 59.0×21.6(9.0) inch |
8,250 mm 324.8 inch |
10,295 mm 405.3 inch |
3,440 mm 135.4 inch |
1,730 mm 68.1 inch |
|
TLMX-1201 | 12 | 1 | 1 | 645 | 680×645(290) mm 26.7×25.3(11.4) inch |
645 mm 25.3 inch |
2,700 mm 106.3 inch |
1,790 mm 70.4 inch |
1,540 mm 60.6 inch |
TLMX-1202 | 12 | 2 | 2 | 645 | 680×645(290) mm 26.7×25.3(11.4) inch |
1,290 mm 50.7 inch |
3,345 mm 131.6 inch |
1,790 mm 70.4 inch |
1,540 mm 60.6 inch |
12 | 2 | 2 | 645 | 1,200×645(290) mm 47.2×25.3(11.4) inch |
1,290 mm 50.7 inch |
3,345 mm 131.6 inch |
2,830 mm 111.4 inch |
1,540 mm 60.6 inch |
|
TLMX-T0908 | 9 | 8×2 | 8 | 745 | 1,200×745(425) mm 47.2×29.3(16.7) inch |
5,960 mm 234.6 inch |
8,570 mm 337.4 inch |
2,840 mm 111.8 inch |
1,630 mm 64.1 inch |
TLMX-T1204 | 12 | 4×2 | 4 | 840 | 1,200×840(485) mm 47.2×33.0(19.0) inch |
3,360 mm 132.2 inch |
6,210 mm 244.4 inch |
2,840 mm 111.8 inch |
1,630 mm 64.1 inch |
*Stitch length 0.1-12.7mm
*Maximum speed
Standard heads Standard embroidery Max.1,000rpm
Lock-stitch chenille heads Taping / Zigzag swing stitch embroidery Max.1,000rpm Coiling embroidery Max.500rpm
*Power supply
3-phase 200-240 / 350 / 380 / 400 / 415 / 440V 50/60Hz
*Power consumption 2.1kw
*Contact us for other specifications and more details.
*The actual embroidery field and embroidery speed may vary depending on the items being produced, the machine model, and the embroidering conditions.
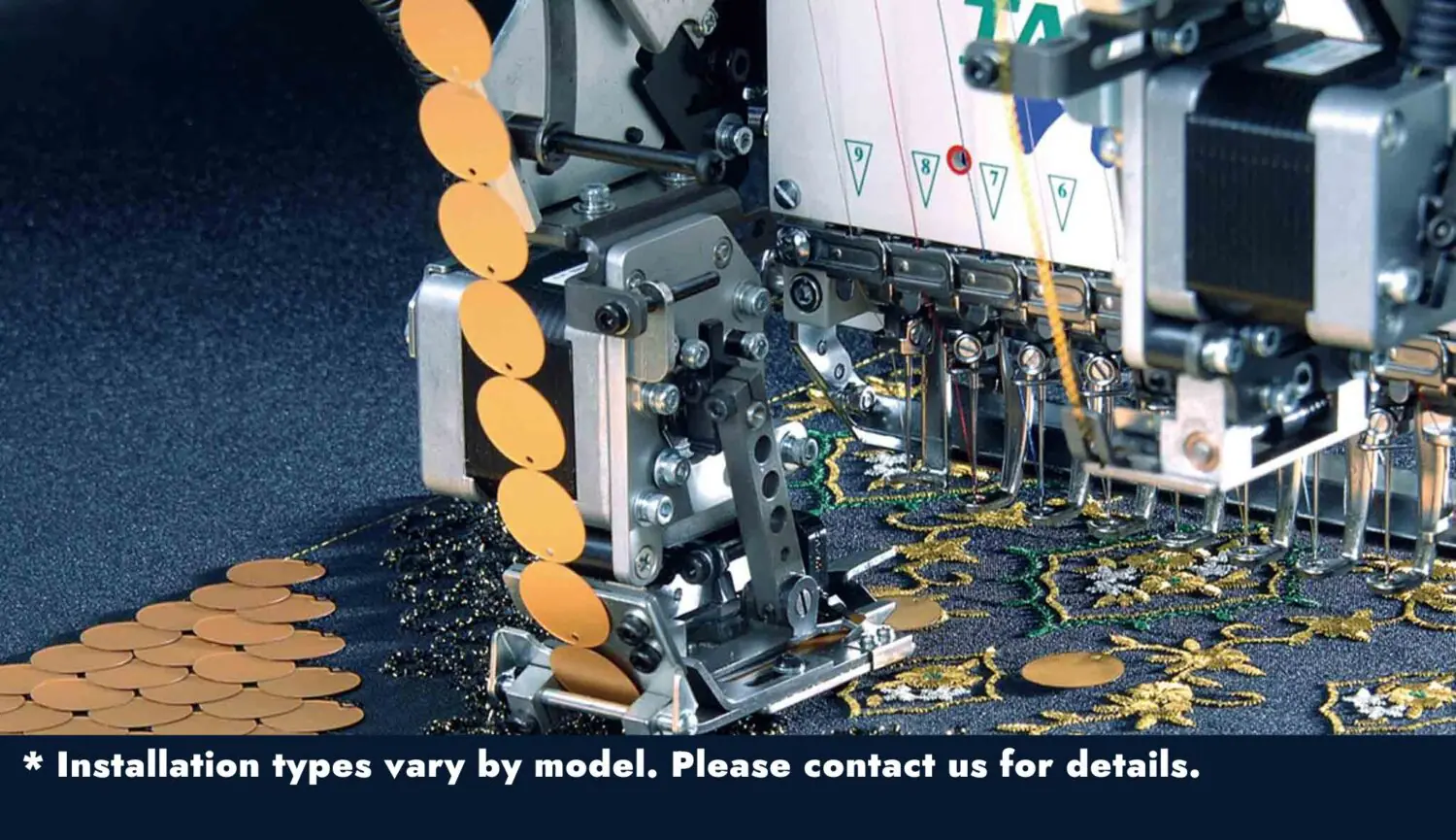
Sequin Device
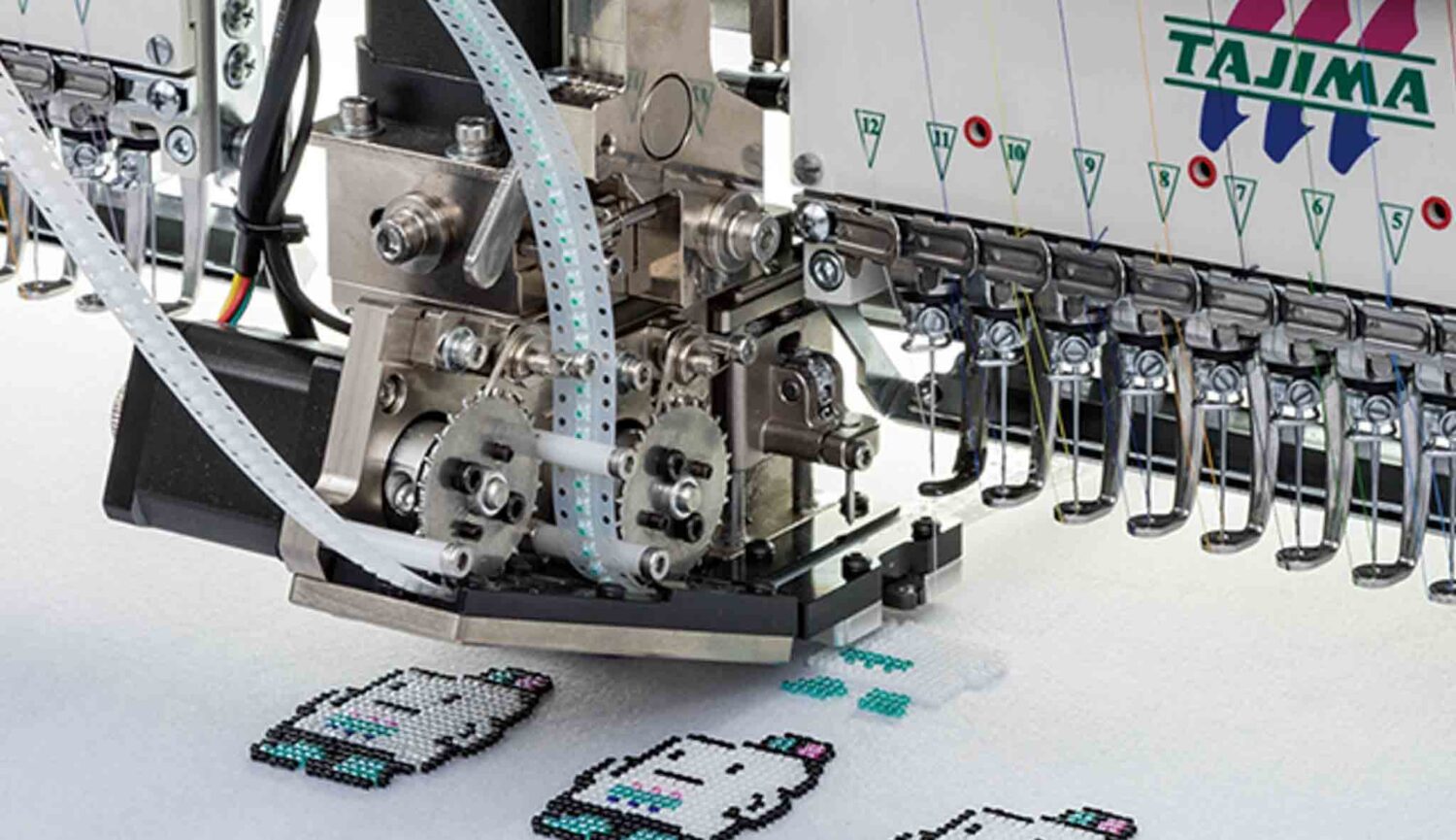
Seed Beads Device
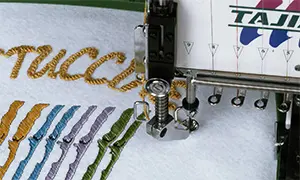
KB-2M

Beam Sensor
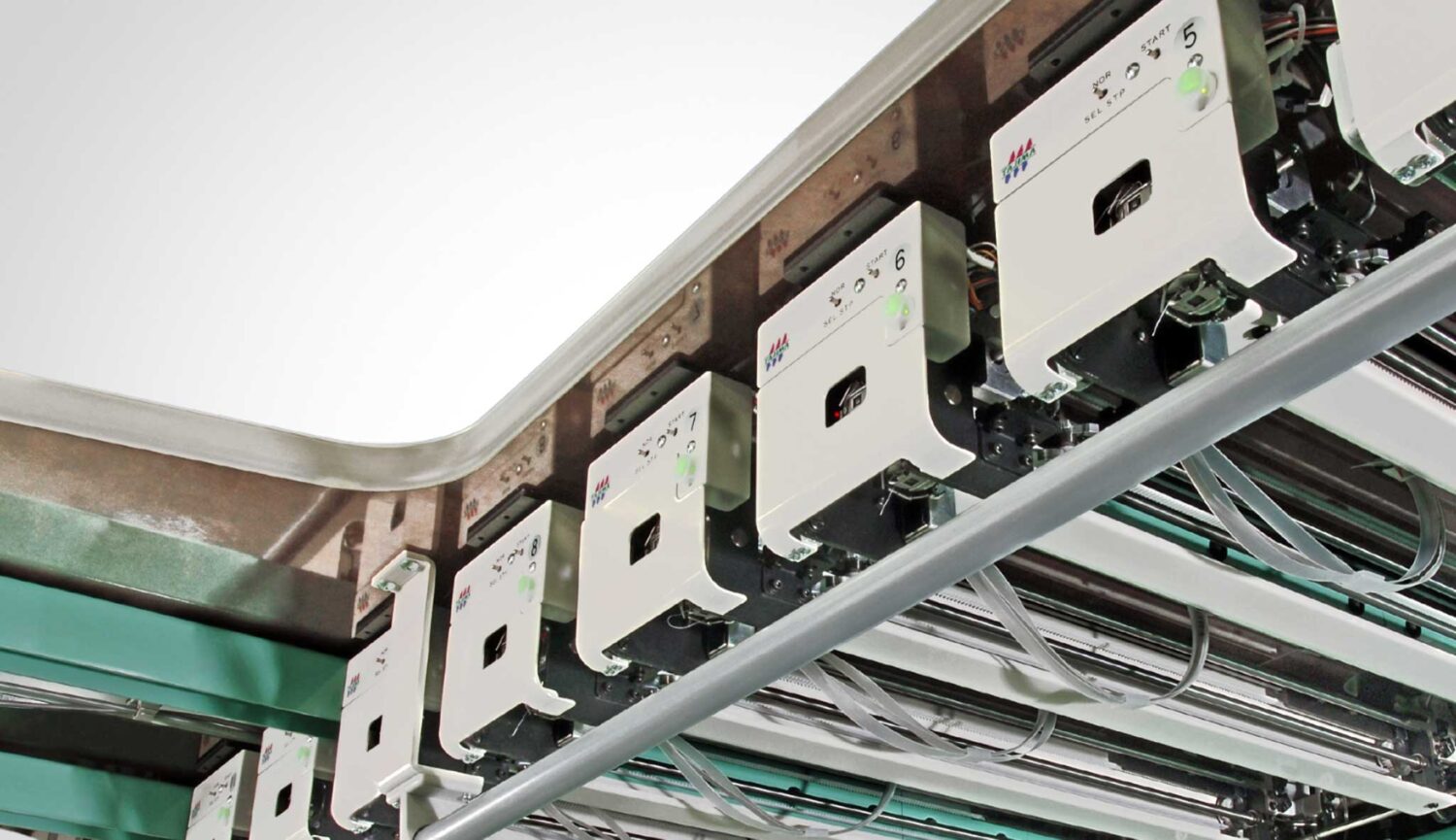
Bobbin Changer(Only Mix Type)
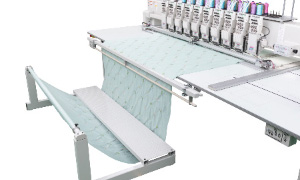
AFC
TLMX 100
Model | Lock-stitch chenille heads |
Head interval |
Embroidery field (D×W) | Embroidery field (Continuous) | Overall Width | Depth | Height |
---|---|---|---|---|---|---|---|
TLMX-112 | 12 | 500 | 1,200×500 mm 42.7×19.6 inch |
6,000 mm 236.2 inch |
7,450 mm 293.3 inch |
2,840 mm 111.8 inch |
1,630 mm 64.1 inch |
*Stitch length 0.1-12.7mm
*Maximum speed
Lock-stitch chenille heads Taping / Zigzag swing stitch embroidery Max.1,000rpm Coiling embroidery Max.500rpm
*Power supply
3-phase 200-240 / 350 / 380 / 400 / 415 / 440V 50/60Hz
*Power consumption 1.9kw
*Contact us for other specifications and more details.
*The actual embroidery field and embroidery speed may vary depending on the items being produced, the machine model, and the embroidering conditions.
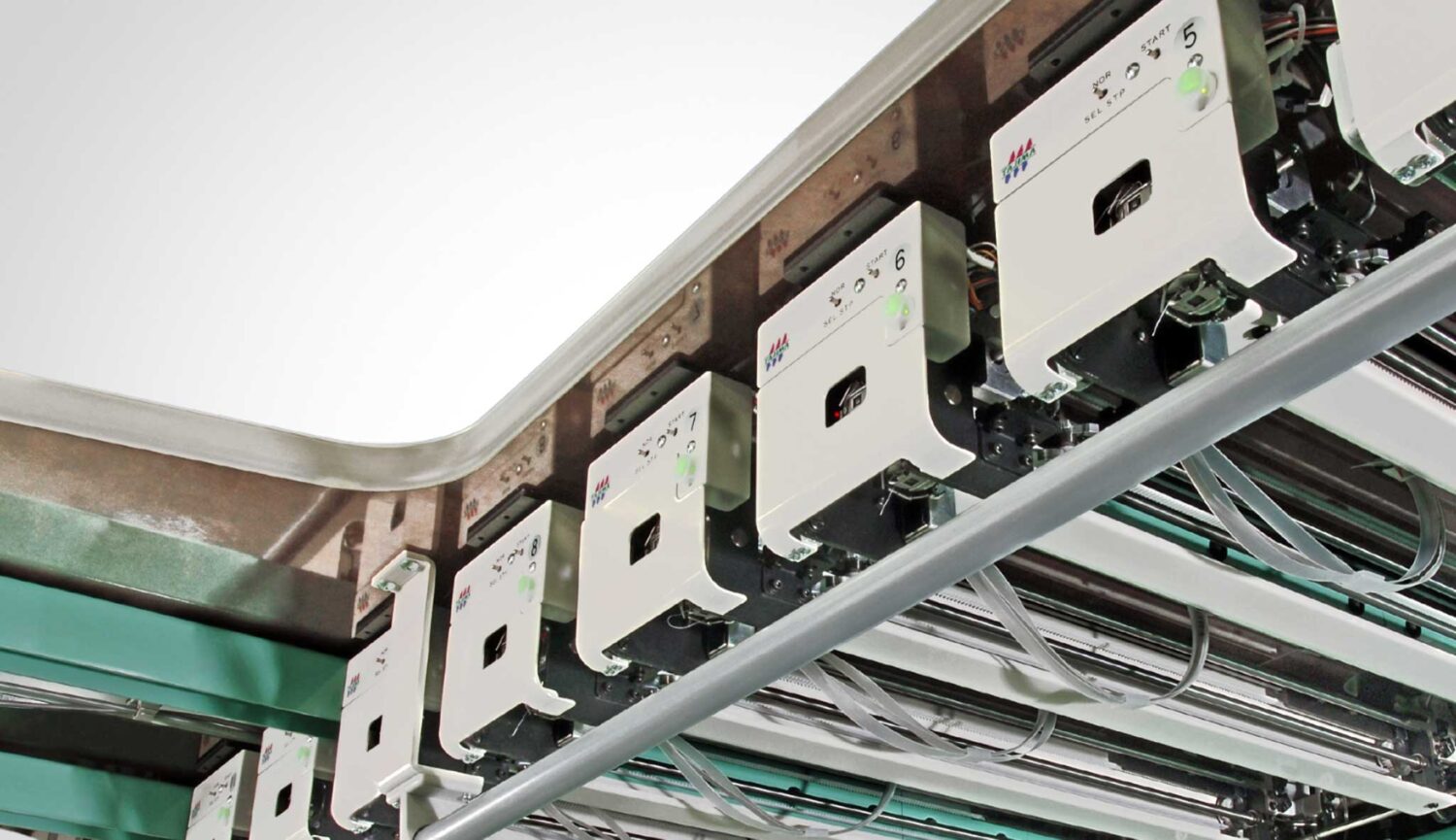
Bobbin Changer

Beam Sensor
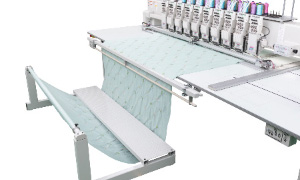
AFC
TLMX Heater Wire Sewing
Model | Lock-stitch chenille heads |
Head interval |
Embroidery field (D×W) | Embroidery field Continuous(w) |
Overall Width | Depth | Height |
---|---|---|---|---|---|---|---|
TLMX-101 | 1 | 800 | 800×800 mm 31.5×31.5 inch |
800 mm 31.5 inch |
2,145 mm 84.4 inch |
2,030 mm 79.9 inch |
1,690 mm 66.5 inch |
TLMX-110 | 10 | 600 | 1,200×600 mm 42.7×23.6 inch |
6,000 mm 236.2 inch |
8,215 mm 323.4 inch |
2,840 mm 111.8 inch |
1,680 mm 66.1 inch |
TLMX-T01 | 1×2 | 875 | 750×875(325) mm 29.5×34.4(12.8) inch |
875 mm 34.4 inch |
3,495 mm 137.6 inch |
1,940 mm 76.3 inch |
1,690 mm 66.5 inch |
TLMX-T08 | 8×2 | 750 | 1,200×750(195) mm 47.2×29.5(7.6) inch |
6,000 mm 236.2 inch |
8,160 mm 321.2 inch |
2,840 mm 111.8 inch |
1,680 mm 66.1 inch |
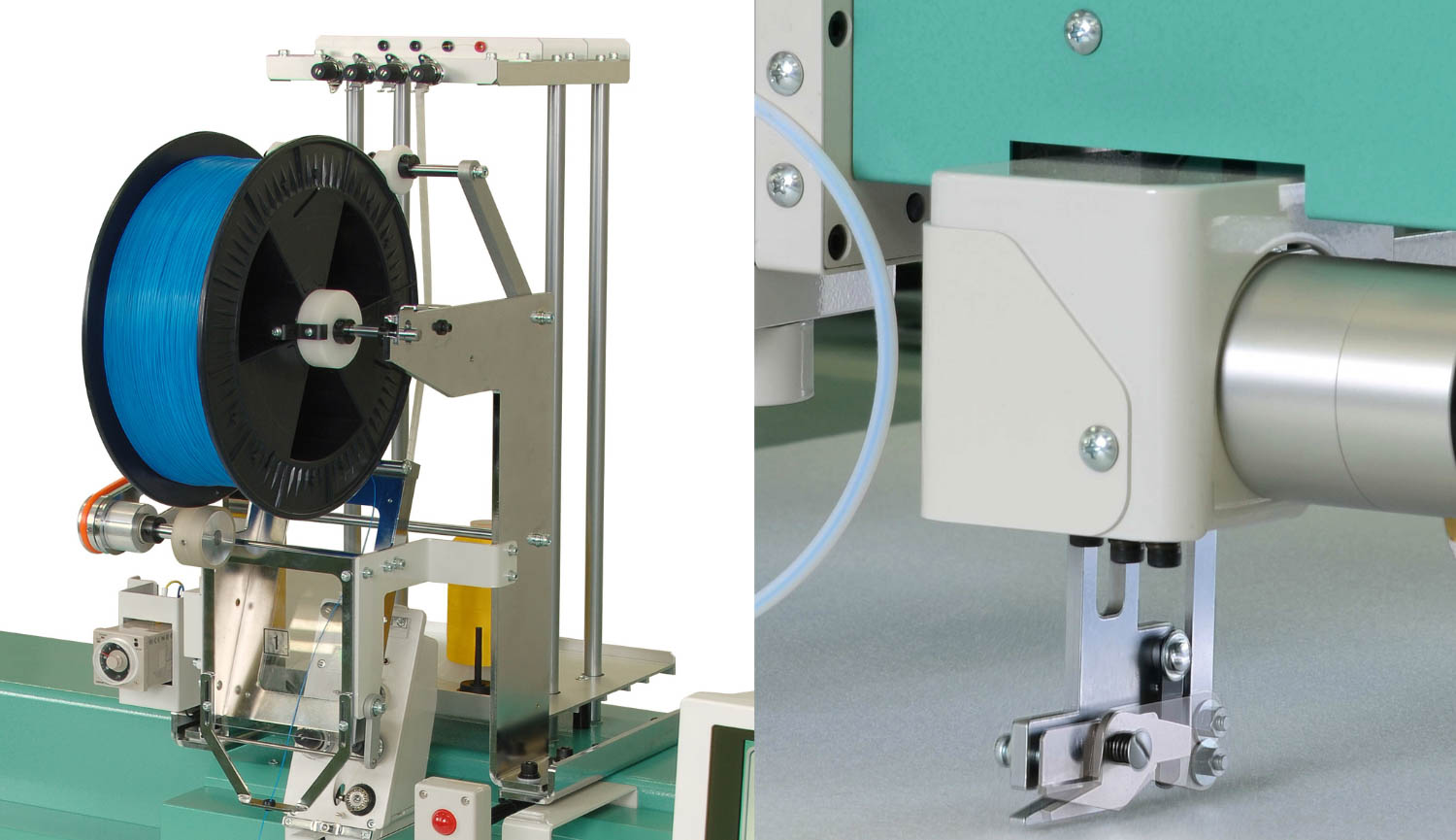
Heater Wire Feeding DeviceHeater Wire Cutting Device
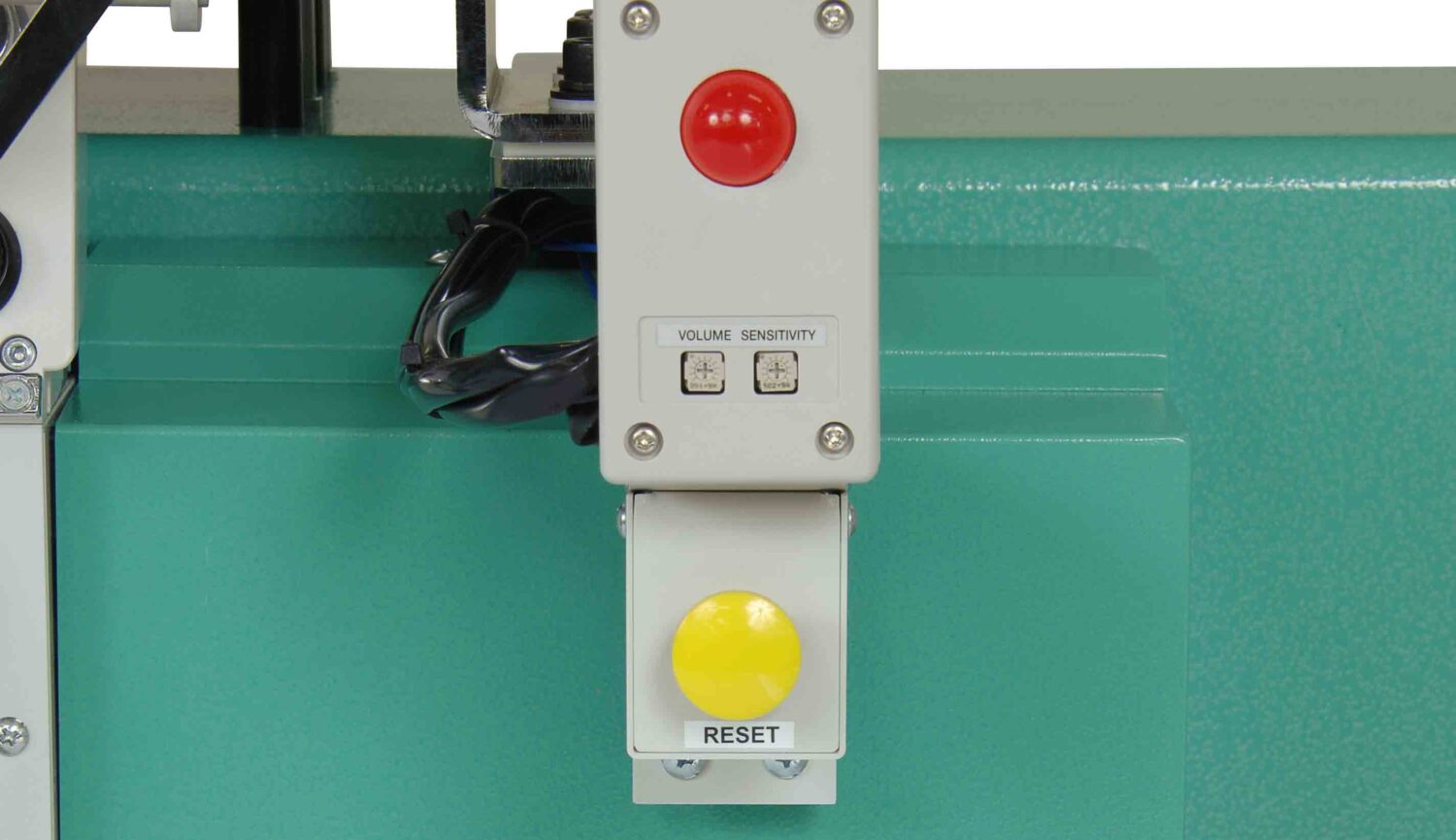
Needle Contact Detection Device
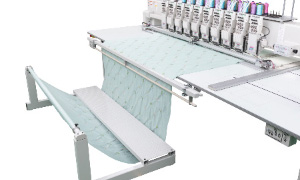
AFC

Beam Sensor
Catalog Download
Distributors
TAJIMAG
Recommended content