Maximizing the properties of carbon fiber and
other reinforced fiber materials
Many industries in recent years have come to use carbon fiber reinforced polymers (CFRP) that leverage carbon’s properties of strength and lighter weight. With the use of CFRP continuing to grow in the fields of aerospace, industry, sports, and other domains, the Tajima Group now offers process that maximize CFRP’s properties and further reduce the material’s weight while increasing its rigidity.
TFP process enables the free arrangement of fibers to create unique materials
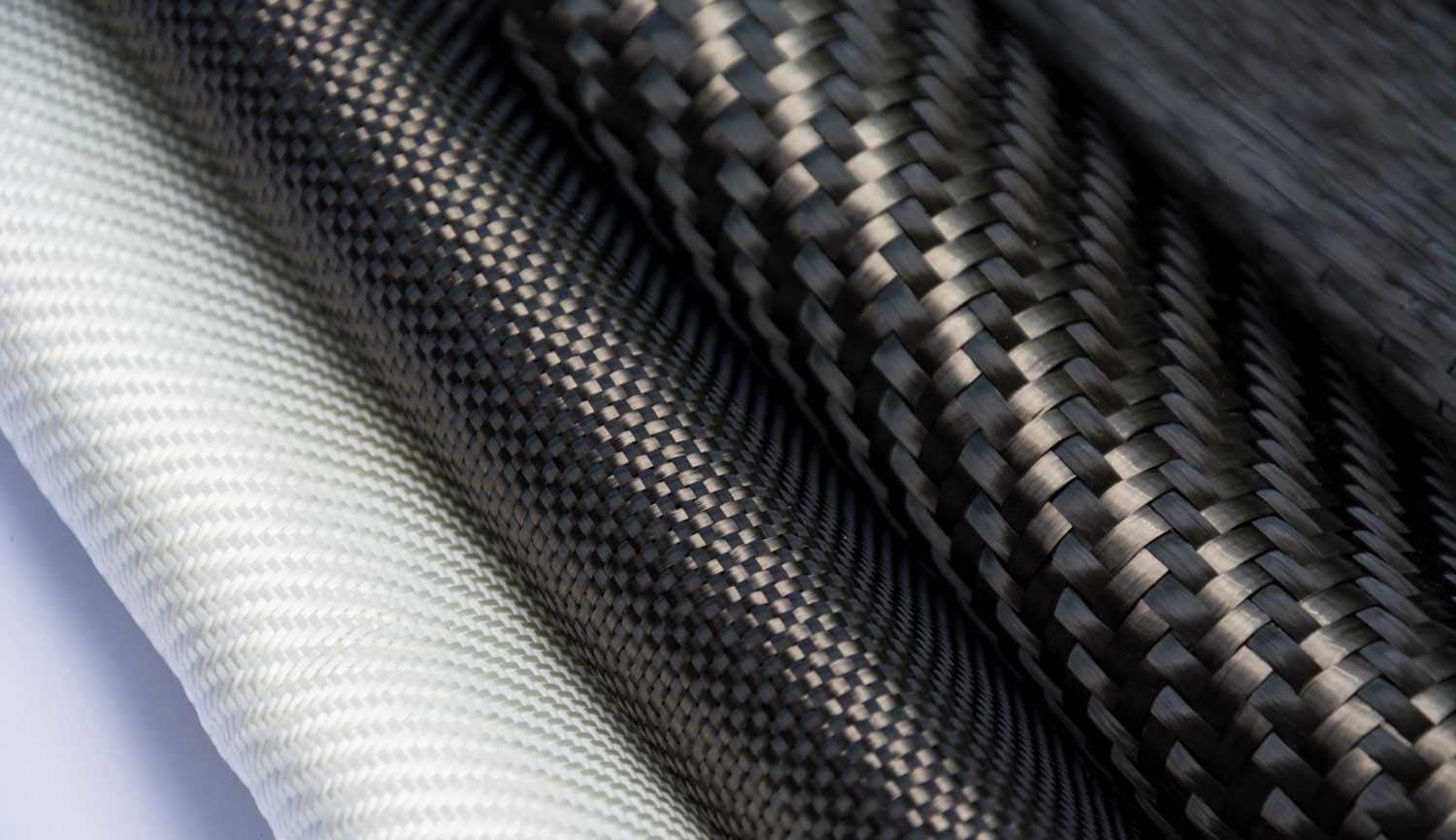
Molding preforms from CFRP generally involves use of unidirectional tape or sheet materials. However, reinforced fibers have pronounced anisotropic characteristics, i.e., they provide strength only in the direction of the fiber’s orientation, so to maximize the material’s properties, fibers need to be oriented along the lines of principal stress. While such conventional unidirectional tape and textile materials are sufficient when the stresses are oriented at 0° or 90°, they are extremely difficult to use on hollow, spiral, radial, and other more complex shapes, creating major challenges both in terms of manufacturing and strength.
In response, Tajima uses the TCWM Spec.2 tailored fiber placement machine, which was developed from Tajima’s core embroidery technology, and the TFP (Tailored Fiber Placement) process, which was developed academic-industrial alliance. This approach allows fibers to be sewn freely onto toroidal, radial, and other forms, with the fibers arranged and concentrated in areas as needed to produce the required degree of strength. In other words, the TFP process resolves the issues encountered in manufacturing by freely arranging fibers based on the particular purpose and creating totally unique materials.
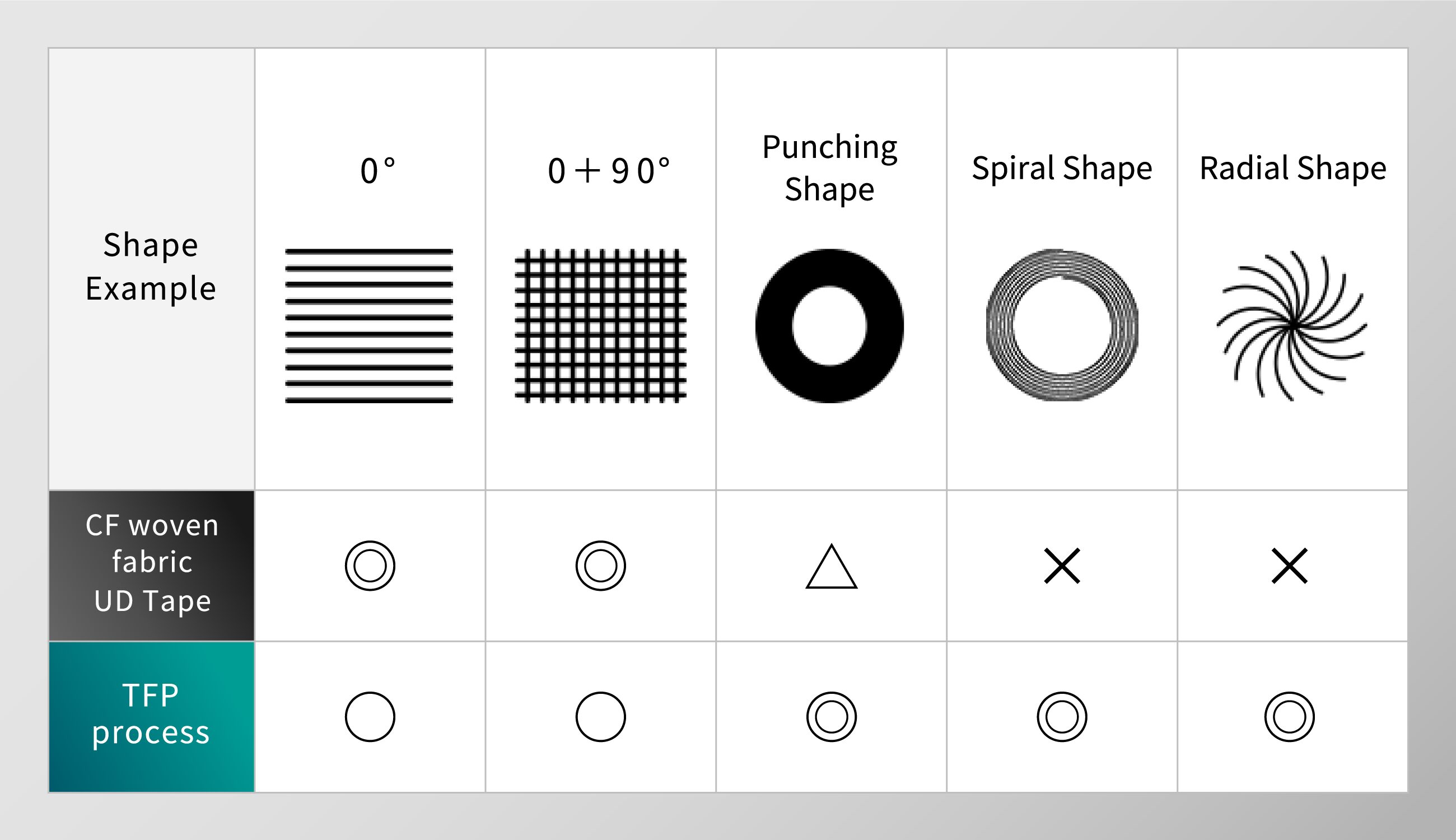
Freedom to orient fibers in the principal direction of stress opens the door to replacements for metal parts
When replacing metal parts with CFRP, using the TFP process rather than stacking preforms from unidirectional tape or textile materials more effectively orients the long fibers in the principal direction of stress, drastically increasing rigidity while reducing weight.
[Use case: comparing the rigidity of bicycle brake booster component]
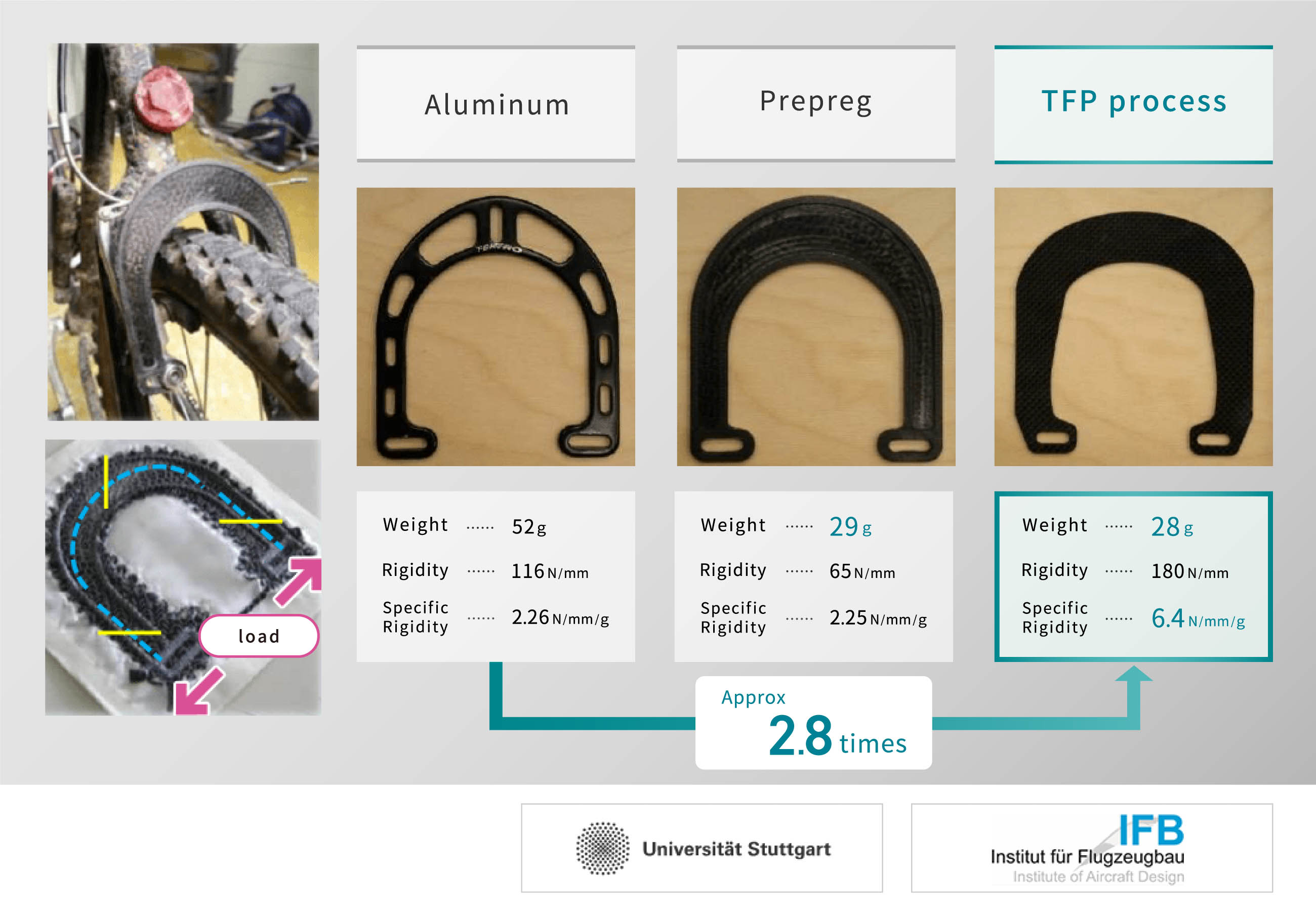
Transcending “common sense” with the TFP process and topology optimization
“Topology optimization” is a process of discovering optimal design plans by eliminating unnecessary material under specific conditions. An ideal design theory that leverages the benefits of weight reduction and greater strength, accordingly, it has come into widespread use in designing plastic and metal components. The optimal structure obtained with this process often includes multiple holes, resulting in a complex shape that cannot be sufficiently achieved using topology optimization with conventional quasi-isotropic CFRP.
In contrast, the TFP process permits free orientation of the fibers. In transcending conventional wisdom of seeking to reduce weight using topology optimization of metal parts, we have created significantly lightweight and highly rigid components from CFRP using the TFP process with a topology-optimized structure.
Manufacturing process with the TFP process
Modeling → (Topology optimization) → CAE analysis → Orientation design → Stitch data conversion
We model the target component and study topology-optimized structures for the particular product. After determining the principal direction of stress and other conditions, we perform CAE analysis to confirm the strength and rigidity. Based on the results of the analysis, we design the fiber orientation, then convert the fiber orientation data into stitch data using the specialized application EDO path Version 2.0.
Generation of the preforms
Based on the stitch data, the reinforcing fibers are sewn onto glass cloth or another base fabric to create the preforms with Tajima’s TCWM Spec.2 tailored fiber placement machine.
Molding
The preforms are stacked in the mold, the mold is closed, and resin is injected into the mold and cured (RTM process).
*We also have developed a track record of using other molding process such as autoclave molding and press molding.
Completion
After the molded product is removed from the mold, it undergoes the appropriate finishing treatment for the intended use.
Support system staffed by specialists
The Tajima Group develops modeling, orientation design, CAE analysis, and other aspects of the TFP process. Our staff of specialists support customers in solving their problems, from prototyping to mass production. Please feel free to contact us.
We welcome the following:
- Those who want to try the TFP process but do not know where to consult
- Those facing issues related to increasing strength and rigidity, and reducing weight
- Those who want to try new techniques to achieve both functionality and great design
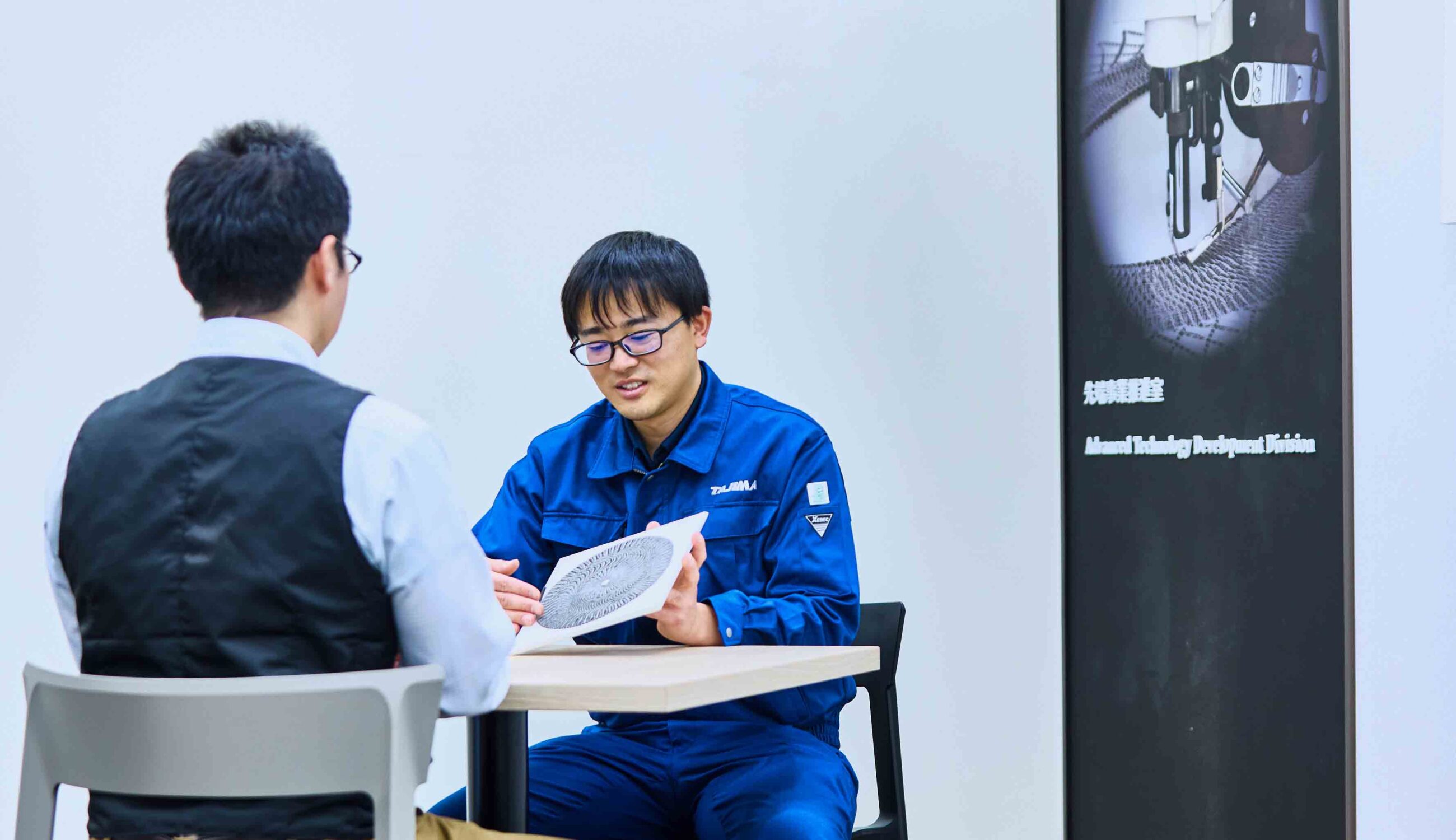
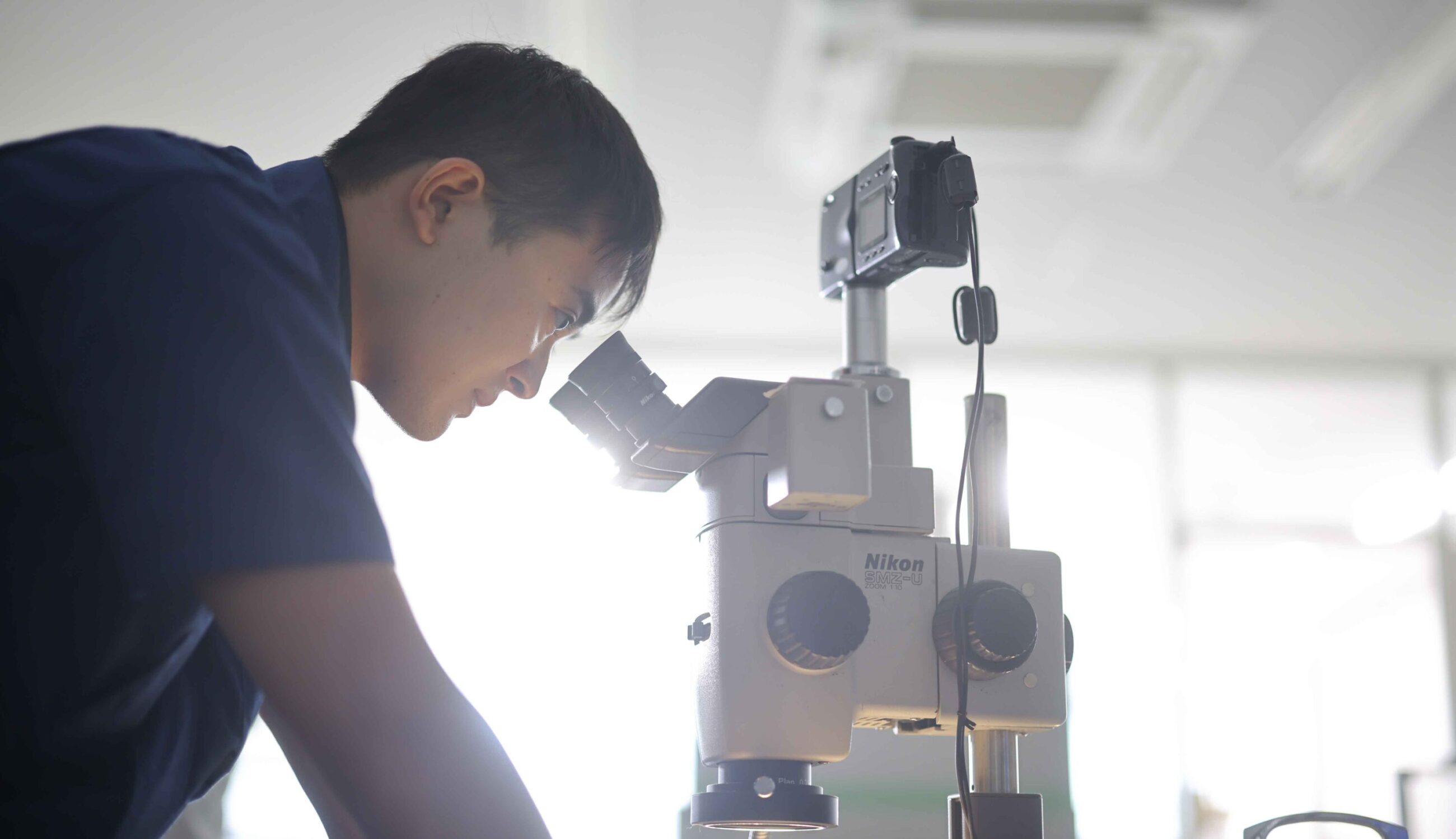
Recommended Products